What is Thermoforming Machine?
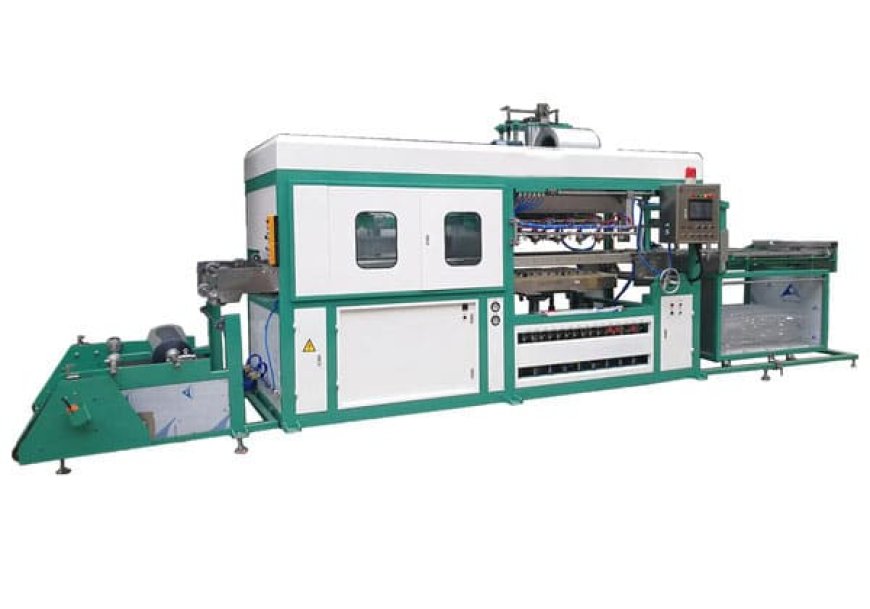
Thermoforming machine is a machine that heats and softens plastic sheet materials, and then adsorbs them on the surface of the mold to form the desired product. It is widely used in the plastic manufacturing process. With the development of science, technology and modern industry, vacuum forming machines are constantly innovating and improving to adapt to market demand.
At present, the thermoforming machine plays a vital role in the production process of plastic products. It has the advantages of low cost, simple operation, and high production efficiency, so it is widely used in daily necessities, industrial products, electronic products and other industries.
As people's awareness of environmental protection increases, the development of thermoforming machines also pays more and more attention to environmental protection and energy saving. Many new thermoforming machines use energy-saving motors and automatic control systems to reduce energy consumption and operating costs. This article will take you to explore more knowledge about pressure forming equipment.
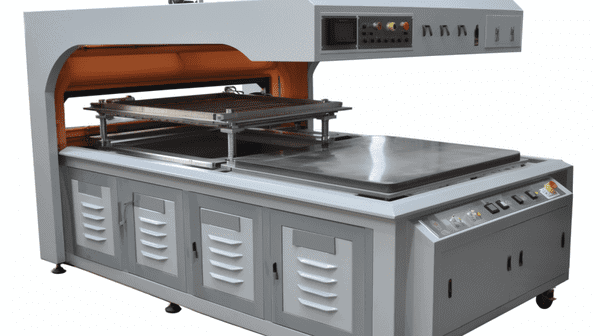
Ⅰ. Thermoforming (Vacuum Forming / Pressure Forming)
Thermoforming Principle
Thermoforming process is a plastic sheet (plate) forming processing technology, which is one of the plastic secondary processing industrial technologies. It is different from one-time processing processes such as injection molding and extrusion. It does not heat mold the plastic resin or particles or continuously mold the same cross-section with the mouth mold. Instead of using machine tools, cutting tools and other mechanical processing methods to cut a part of the plastic material to obtain the required shape and size, it is to heated plastic sheet (plate) and use molds, vacuum pressure to make the sheet (plate) The material is deformed to achieve the final shape and size, supplemented by supporting processes to achieve the application purpose.
There are several thermoforming methods used in actual production, and the most basic ones are six: differential pressure forming, overmolding, plunger-assisted molding, vacuum forming, countermolding, and twin sheet forming.
Thermoforming Features
1. Product specifications are highly adaptable. Thermoforming can be used to produce various products of extra large, extra small, extra thick, and extra thin. The thin gauge thermoforming sheet thickness can be as thin as 1-2mm, or even thinner, and the thick gauge thermoforming sheet can be as thick as 20mm. The product area can be as large as 10 square meters or as small as a few square millimeters.
2. Products are widely used in daily necessities vacuum forming packaging, small hardware thermoforming packaging, automotive supplies thermoforming packaging, electronic product thermoforming packaging, food thermoforming packaging, cosmetic thermoforming packaging, computer peripheral equipment thermoforming packaging, toy thermoforming packaging, thermoforming packaging for sporting goods, thermoforming packaging for stationery, etc.
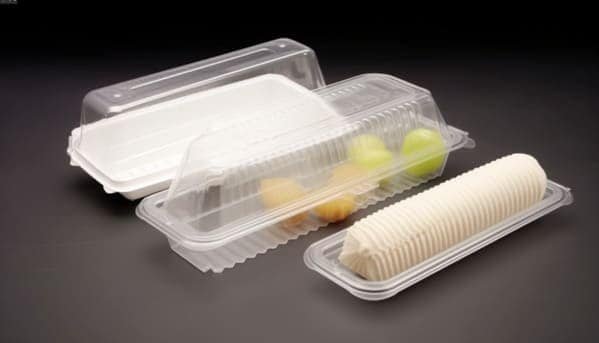
3. Low equipment investment.
4. Mold manufacturing is convenient (including plaster molds, copper molds, aluminum molds, etc.).
5. High production efficiency, saves raw and auxiliary materials, is light in weight, easy to transport, has good sealing performance, and meets the requirements of environmentally friendly green packaging. It can pack any special-shaped products, and no additional buffering materials are needed for packaging. The packaged products are transparent and visible, beautiful in appearance, easy to sell, and suitable for mechanized and automated packaging, which facilitates modern management, saves manpower, and improves efficiency.
Ⅱ. Thermoforming Machine
Thermoforming Machine Principle
Thermoforming machine is a machine that absorbs heated and plasticized thermoplastic plastic rolls such as PVC, PE, PP, PET, HIPS, etc. into various shapes of advanced packaging and decoration boxes, frames and other products.
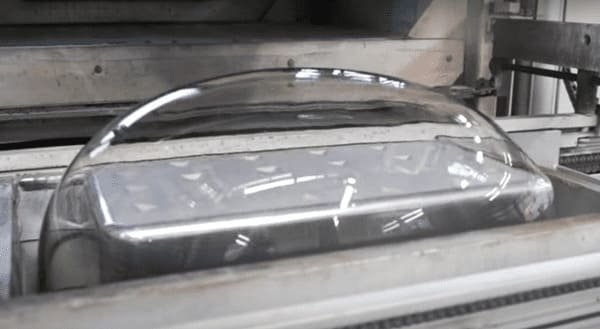
Principle of thermforoming machine: thermoforming is also called thermoplastic molding. This forming process mainly uses the vacuum suction generated by a vacuum pump to heat and soften thermoplastic plastic sheets such as PVC, PET, PETG, APTT, PP, PE, and PS. Process materials into various shapes of vacuum films, thermoformed trays, blisters, etc.
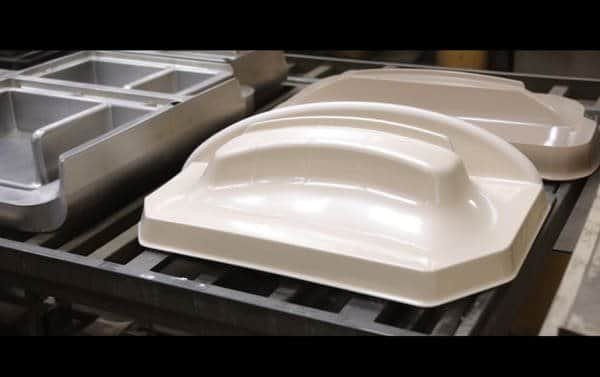
Thermoforming Machine Structure
Thermoforming equipment includes clamping systems, heating systems, vacuum and compressed air systems, and forming molds.
The main structure of thermoforming machine is composed of feeding, pulling, upper and lower electric heating furnaces, lower gate, multi-functional adjustable size, lower mold plate, upper mold, upper gate, knife gate, slicing, releasing and vacuum device, etc. constitute. The pneumatic device is the main power source, and the puller and feeder adopt electric, reducer, time relay, intermediate relay, travel switch and other electrical appliances to form a fully automatic control system.
The requirements for the control system of thermoforming machine are to ensure easy operation, high precision in mechanical action and temperature control, short production time, and save the power consumption of the machine as much as possible under the same production conditions.
Application
Plastic packaging industry: thermoforming packaging, plastics, batteries, toys, gifts, hardware, home appliances, electronics, stationery, decoration.
Food packaging industry: fast food boxes, fruit trays, biscuit boxes.
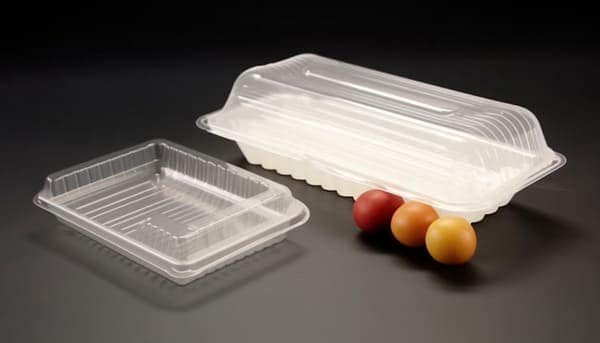
Pharmaceutical industry: pill packaging, tablet packaging.
Industrial cooling tower cooling water deflector, etc.
Manufacturing industries such as decorative three-dimensional relief patterns, plastic ceilings, wall panels, automotive materials, and sanitary equipment.
Suitable for producing sheets of various colors: polyethylene PS, polyvinyl chloride PVC, plexiglass, ABS, polymethylmethacrylate. Flocking sheet. Environmentally friendly sheets APET, PET, PP, etc. Photodegradable materials. Biodegradable materials and other plastic products.
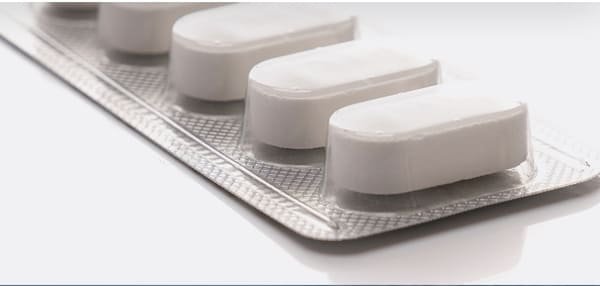
Ⅲ. Composition and Function of Thermforoming Equipment
Clamping Device
When the plastic sheet is formed, the sheet is held in place on a clamping device. Clamping devices that facilitate the fixation of sheets of various sizes are often used on general-purpose and composite thermoforming machines. Some have the entire molding machine equipped with a clamping frame.
Clamping devices can be divided into two categories: one is frame type and the other is split type. The frame-type clamping device consists of upper and lower frames. The sheet is sandwiched between two frames. When the frame is open, the lower frame generally remains fixed.
The lower part of the upper frame of various types of single-station molding machines is directly fixed on the molding chamber. Manual and semi-automatic molding machines for loading parisons and removing finished products by hand, when the frame size is large, are equipped with safety operating devices within the frame opening range.
For parisons with large slippage during molding, the clamping force is required to be adjusted within a relatively wide range. To this end, two rubber-covered rollers are used to press each other with springs and are equipped with a pressure adjustment device. The clamping of the continuous pull tab forming machine is the joint action of the zippers on both sides and the front and rear gates.
It is best to use automatic control for the clamping device so that it can act quickly and help improve the quality and efficiency of the parts.
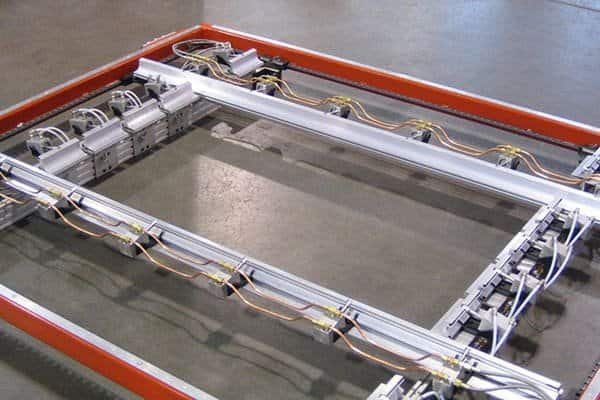
Heating Equipment
One of the main processes in the vacuum forming process of thermoplastic sheets and films is sheet heating. The duration and quality of electric heating depend on the structure of the heater, the thermal inertia of temperature heat transfer behind the radiating surface, the distance between the sheet and the heater, the radiant energy absorption coefficient, the characteristics of the heater surface and the thermophysical properties of the material. Commonly used heaters include electric heaters, crystal radiators and infrared heaters.
Vacuum System
The vacuum system consists of a vacuum pump, a gas tank, valves, pipelines, and a vacuum meter. In vacuum molding, a separate vacuum pump is often used. The vacuum degree of this pump should reach 0.07~0.09 Mpa (520mmHg) or above. The gas storage tank is generally a cylindrical box welded with thin steel plates, with an oval bottom. The capacity of the gas tank should be at least half greater than the capacity of the largest molding chamber. On the vacuum line, appropriate valves must be installed to control the narrow vacuum capacity.
The rotational power of the vacuum pump is determined by the size and molding speed of the molding equipment. Larger or faster molding speed equipment is often as large as 2-4KW. The size of the vacuum central system depends on the specific production and development requirements of the factory.
Air Compressor
The pneumatic system can be composed of the molding machine itself with a compressor, a gas storage tank, a workshop main pipeline set, valves, etc. The forming machine requires compressed air with a pressure of 0.4-0.5MPa, and piston air compressors are widely used in various vacuum forminging machines. Large spiral air compressors can also be supplied from the whole factory.
In addition to being used in large quantities for molding, compressed air is also partially used for demoulding, external cooling of the initial product, and power to control the movements of the mold frame and running sheets.
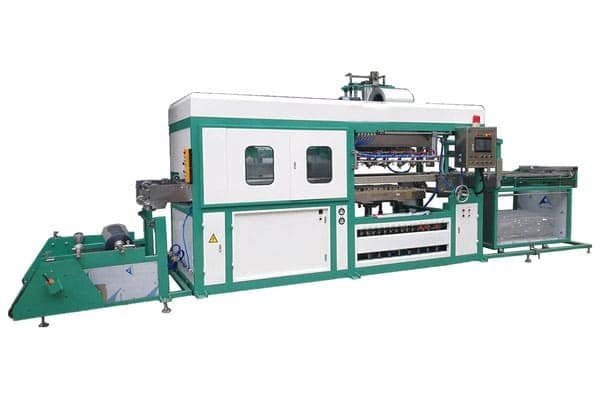
Cooling Equipment
In order to improve production efficiency, vacuum forming products often need to be cooled before demoulding. Ideally, both the inner and outer surfaces of the part in contact with the mold are cooled, and it is best to use a mold with a built-in cooling coil. For non-metal molds, such as wood, gypsum, glass fiber reinforced plastic, epoxy resin and other molds, since water cannot be cooled, air cooling can be used instead, and additional water mist can be added to cool the outer surface of the thermoforming parts.
If natural cooling is used during production, annealed parts can be obtained, which is beneficial to improving the impact resistance of the parts. Although water cooling has high production efficiency, the internal stress of the parts is relatively large.
Demoulding Equipment
Demolding is to move the product out of the mold, usually whether it is a concave mold or a male mold. In most cases, the product is close to the mold due to cooling and shrinkage, so it is demolded through a vacuum suction hole or blowing in the opposite direction.
Especially for molds with small demoulding slopes or molds with concave molds, the demoulding mechanism is used to push or vibrate the mold at the same time. Sometimes a release agent is applied to the sheet and the mold or the surface of the mold is sprayed with Teflon.
Controlling Device
The control system generally includes the control of various parameters and actions of instruments, meters, pipes, and valves during vacuum forming, finishing, and other processes. Control methods include manual, electrical-mechanical automatic control, computer control, etc. The specific selection should be comprehensively considered based on the initial investment in labor costs, technical requirements, raw material costs, production and maintenance equipment costs and other factors.
Ⅳ. Commonly Used Plastics and Properties of Thermforming Machine
Plastics can be divided into two categories: thermoplastics and thermosetting plastics according to their heating behavior. Most of the materials used in thermoforming machines are thermoplastic materials.
Whether single-layer or multi-layer composite plastic sheets (plates) used for thermoforming processing must have the following process properties:
1. Plastic memory
2. Heat stretching
3. Heat intensity
4. Forming temperature
Commonly Used Plastics for Thermoforming Machine
1. PVC. PVC sheets have low impurity content, good transparency, low price, good dielectric properties, flame retardancy and self-extinguishing properties.
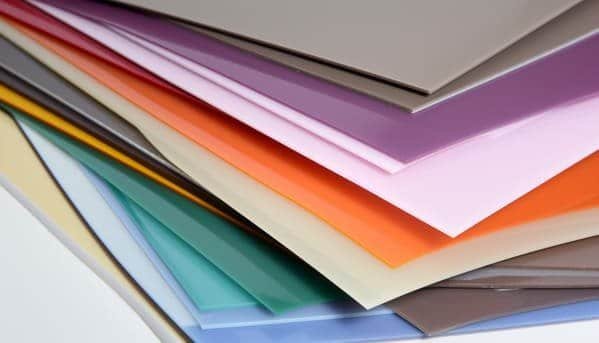
2. PP. PP sheets are abundant in sources, cheap in price, excellent in performance, and widely used. Has the following characteristics:
Low density, PP is colorless, odorless, tasteless, non-toxic, flammable, white in appearance and density is 0.90-0.91g/㎝³.
Good mechanical properties. PP has particularly good rigidity, elongation, and good resistance to stress cracking.
Better heat resistance.
Good chemical stability.
Transparency, good water and waterproof properties.
Easy to process and easy to use.
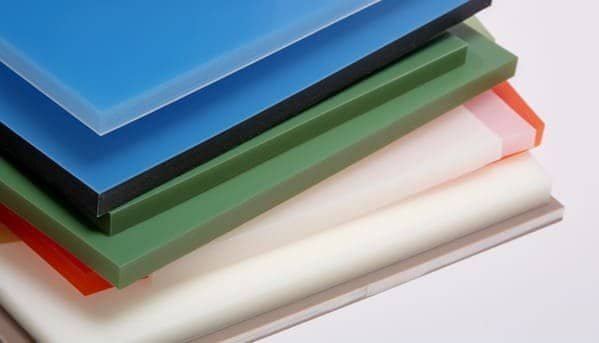
3. PE. PE is currently one of the most widely produced and widely used plastic varieties. It is odorless, tasteless, non-toxic and flammable.
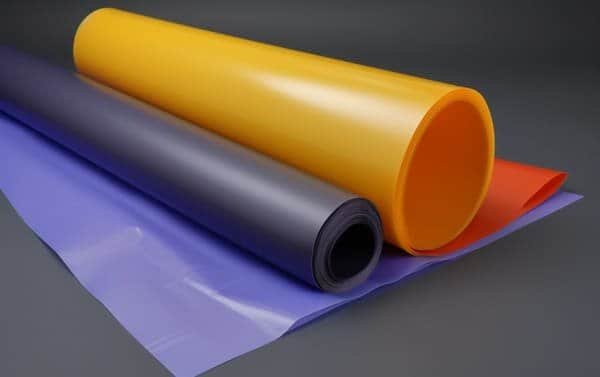
4. PS. PS sheet material is hard, brittle, transparent, odorless, emits black smoke when burned, easy to dye and process, has low hygroscopicity, dimensional stability, and good electrical and thermal insulation.
Advantage:
High transparency and gloss.
Colorability and hygienic performance are excellent.
Excellent dielectric properties.
Excellent molding performance.
Disadvantages:
Material is brittle.
The heat resistance is poor.
Moisture-proof and poor oxygen barrier.
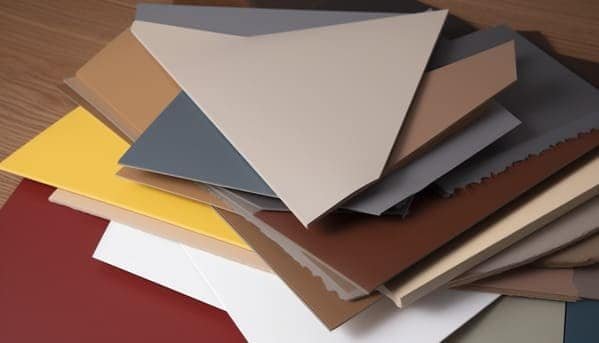
5. ABS. ABS sheets are opaque, non-toxic and odorless.
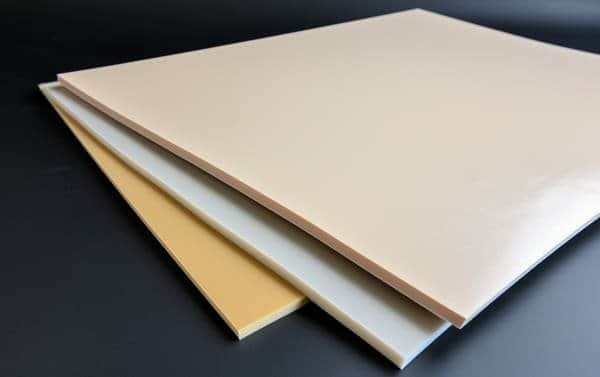
6. PET. PET is colorless, odorless, tasteless, non-toxic, has excellent transparency, excellent mechanical strength, wear resistance and electrical insulation properties, good creep resistance, rigidity and strength. Excellent hygiene allows it to come into direct contact with food.
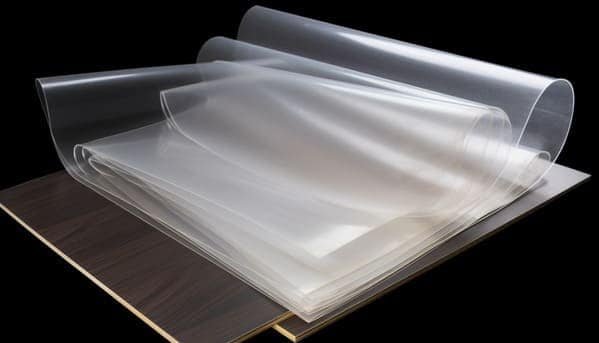
Ⅴ. Conclusion
As an important force in the modern industrial field, thermoforming packaging equipment automation is gradually changing the face of traditional production methods. With the continuous advancement of science and technology and increasingly fierce market competition, in order to improve production efficiency, reduce costs, and improve product quality, the development trend of automation of vacuum forming packaging equipment has become increasingly obvious.
In short, the automation of air pressure forming packaging equipment is an important trend in future industrial development and is of great significance for improving production efficiency, reducing costs, and improving product quality. Although there are still some challenges, with the continuous advancement of technology, I believe that the future of thermoforming packaging equipment automation will be brighter.
What's Your Reaction?






