The Most Complete Summary of Thermoforming
Thermoforming process is a kind of processing method to adsorb the plastic sheet or plastic film on the surface of the mold through suction after heating and softening, and then form the required products after cooling. Thermoforming process has the advantages of low cost, high production efficiency, short production cycle, and so on, so in the modern industrial production has been widely used.
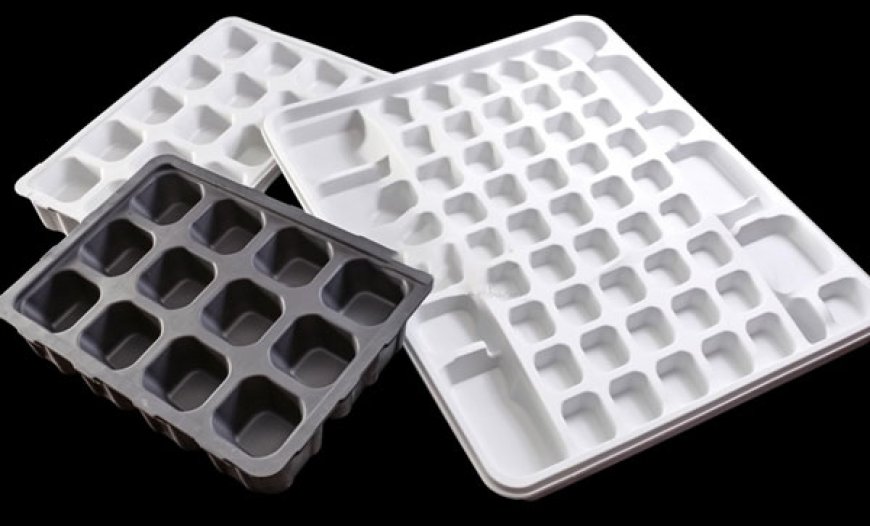
Thermoforming process is a kind of processing method to adsorb the plastic sheet or plastic film on the surface of the mold through suction after heating and softening, and then form the required products after cooling. Thermoforming process has the advantages of low cost, high production efficiency, short production cycle, and so on, so in the modern industrial production has been widely used.
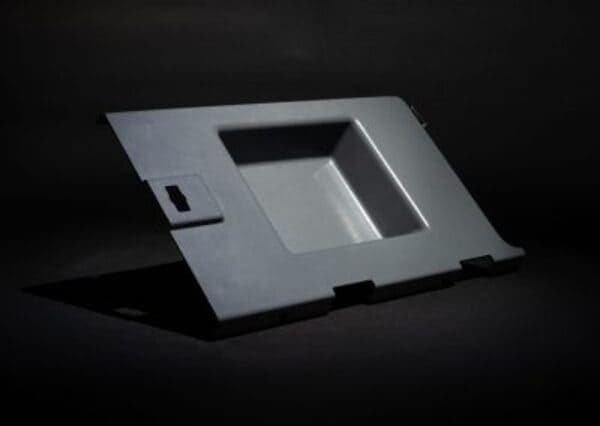
Through continuous development and changes, the vacuum forming process has now become highly automated and mechanized. Through continuous improvement of the vacuum forming equipment, we have improved the temperature control of the vacuum forming machine and the technical difficulties of the transmission method, and solved the process technology of the high tensile and high-precision vacuum forming products, including solving the problem of the processing technology of different plastic materials as well as the thick sheet materials.
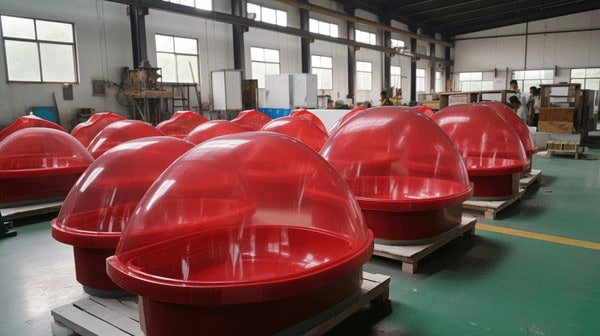
Principles of Thermoforming
Thermoforming is the use of thermoplastic materials, the plastic manufacturing process shell products method, is the plastic sheet cut to a certain size after heating and softening, with the help of the sheet on both sides of the air pressure difference and mechanical pressure, so that the deformation of the deformation of the mold profile in a specific affixed to the surface, after the cooling of the mold, and cut edge trimming to complete the desired shape products process.
There are several thermoforming methods used in actual production, and the most basic ones are six: differential pressure forming, overmolding, plunger-assisted molding, suction molding, countermolding, and twin sheet forming.
In the process, heated sheet, and then the air between it and the mold is quickly extracted, resulting in a vacuum state, forming a pressure difference, so that the plastic sheet is adhered to the mold's molding surface, and then the plastic material is cooled and shaped, and then cut and trimmed to become the required individual products.
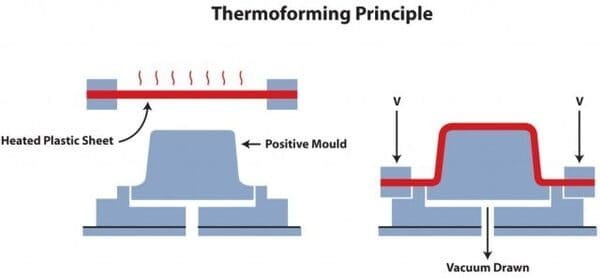
Thermoforming Equipment
Classification According to Sheet Thickness
Thick Gauge Thermoforming
Thick gauge thermoforming common products are: household appliance liner shell, luggage, display rack accessories, decoration, automotive interior, bumpers, fenders, beauty equipment, light box shell, toy car shell, industrial panels, advertising light boxes, thermoforming LOGO, sanitary products, refrigerator liner and so on.
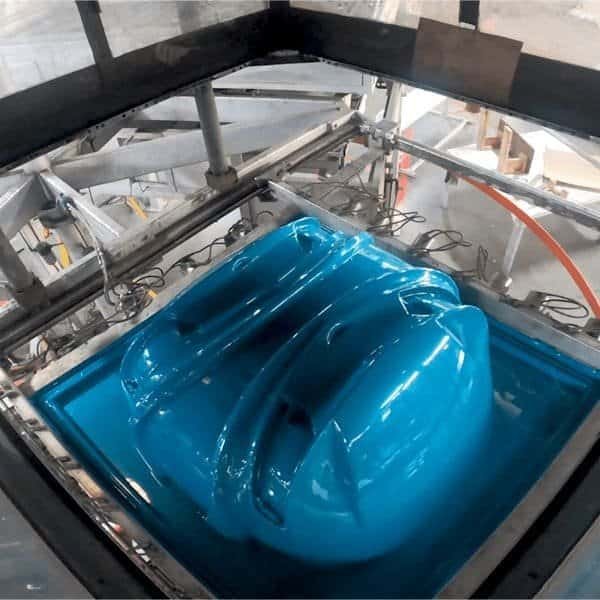
Thin Gauge Thermoforming
The common products on the market are: daily necessities thermoforming packaging, small hardware thermoforming packaging, automotive thermoforming packaging, electronic products thermoforming packaging, food thermoforming packaging, cosmetic thermoforming packaging, computer peripherals thermoforming packaging, toys thermoforming packaging, sporting goods thermoforming packaging, stationery thermoforming packaging and so on.
The main structure of the machine is composed of feeding, pulling, upper and lower electric heating furnace, lower gate, multifunctional adjustable size, lower mold plate, upper mold, upper gate, knife gate, slicing, releasing and with a vacuum device, etc., pneumatic device as the main source of power, and pulling the piece, sending the piece of electric power, speed reducer, time relays, intermediate relays, travel switches and other electrical appliances to form a full-automatic control system.
.jpg)
Different Pressurization Methods
According to the different pressurization methods of thermoforming, the mainstream thermoforming equipment is mainly divided into the following three categories.
1. Vacuum negative pressure thermoforming machine, mainly through the negative pressure vacuum way, makes the plastic material affixed to the mold.
2. Positive pressure thermoforming, through the air compressor on the front of the plastic sheet with atmospheric pressure, so that the softened plastic sheet affixed to the mold.
3. Positive and negative pressure thermoforming machine, is through the way of pressure and vacuum, in the plastic sheet on both sides of the formation of a strong pressure difference, so that the softening of the plastic material molding method.
These three kinds of equipment, each has its own advantages and disadvantages, according to the characteristics of the product on the machine to choose.
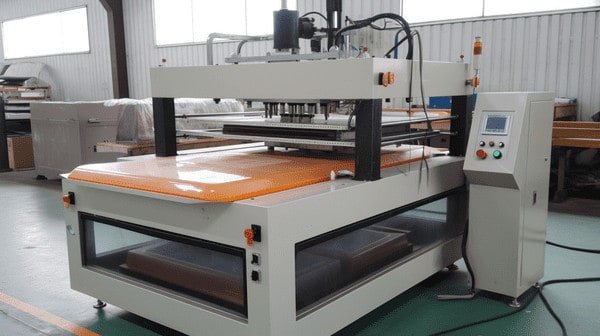
Different Forming Steps
According to the forming steps, thermoforming equipment can be divided into two categories
1. One-step forming machine, is the plastic material heating, plastic absorption forming, die-cutting process into one, high production efficiency, suitable for quality requirements are not high thermoforming products.
2. Two-step forming machine, is the plastic sheet heating, thermoforming process and die-cutting processing separately, suitable for higher quality requirements of thermoformed products.
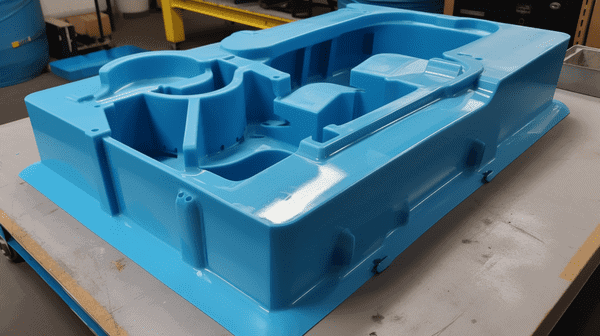
Thermoforming Technology
To produce a good quality plastic products, need to pay special attention to two points: one is the thermoforming mold, the second is the processing requirements.
Mold
Thermoforming molds play a very important role for the advantages and disadvantages of thermoforming products, thermoforming molds can be divided into three kinds of molds: positive mold, negative mold and positive and negative mold.
Both negative and positive mold are a type of plastic processing that uses thermoplastic material to form products through the thermoforming process. The negative mold is characterized by a concave bottom of the mold, and the workpiece is softened by heating above the mold and is adsorbed at the bottom of the mold to form the product. On the other hand, the positive mold is convex at the bottom of the mold, and the workpiece is adsorbed at the top of the mold after being heated and softened underneath the mold to form the product.
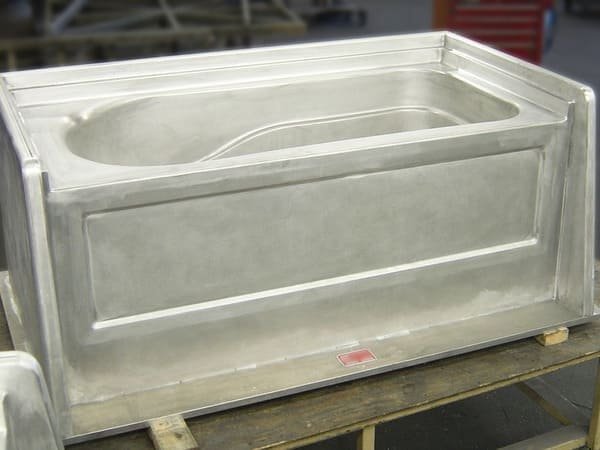
For positive mold, the inner size of the product is very accurate, because it is the side that connects with the vacuum mold tool. On the contrary, for negative mold, the outer dimensions of the part are precise because it is in contact with the vacuum forming tool on the outside.
The negative mold production of the product does not fit with the cavity wall side of the better quality, the thinnest part of the cavity side and the bottom of the junction, and with the increase in the depth of the cavity products at the bottom of the corner of the wall becomes even thinner, so in the processing of deeper products, there should be a correspondingly large opening area.
The maximum part of the wall thickness of the products produced by the male mold is at the top of the male mold, and the thinnest part is at the junction of the side and bottom of the male mold, which is also the last part of the molding process, the side of the products often appear stretching and cooling stripes, resulting in stripes is due to the various parts of the sheet to fit the mold surface, the first part of the first contact with the surface of the die first cooled by the mold and produce stripes, and in the process of the subsequent related to the cavity, is drawn to the sides of the mold cavity. This streaking is usually highest at the sides near the top of the mold face and affects the appearance of the thermoforming product.
Advantages of Positive Mold
1. Product surface is smooth and good quality
2. Low mold investment cost, long mold life
Disadvantages of Positive Mold
1. Only suitable for manufacturing simple geometries;
2. Unable to manufacture larger size workpieces.
3. Since the pattern is pre-made, the pattern effect will be lost during the skin stretching process. Where the stretching is high, the pattern becomes shallow or even disappears.
4. There is a limitation on the R angle of the parts.
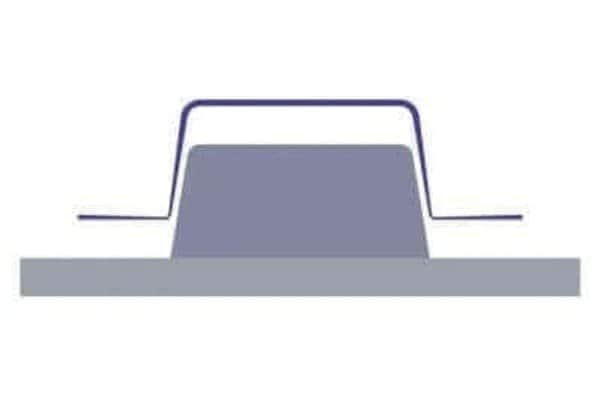
Advantages of Negative Mold
1. Enables the manufacture of more detailed and complex workpieces.
2. Larger size workpieces can be manufactured.
3. Low cost of mold making and use.
4. Better surface pattern effect.
Disadvantages of Negative Mold
1. Lower material utilization rate.
2. Product surface quality may be problematic.
3. Higher mold investment costs and equipment requirements.
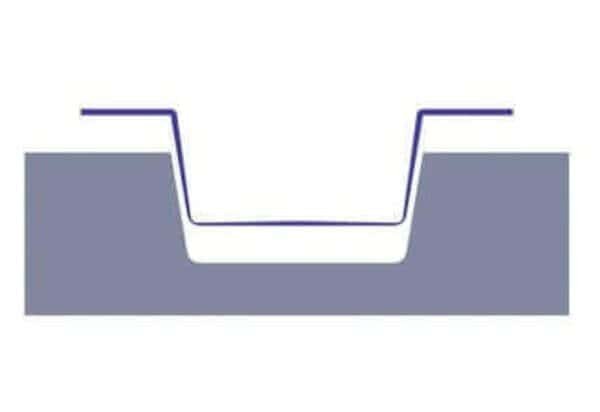
Attention to the Production of Positive Molds
1. When processing with high right angle molds, especially when the height of the mold is high, it is easy to produce draw line wrinkles.
2. Tend to produce cooling streaks at the corners.
3. Uneven wall thickness at the male edge.
4. Difficulty in demolding due to insufficient sidewall slope.
Attention to the Production of Negative Molds
1. Uniformity of edge thickness.
2. Thinner corner parts should be carefully watched not to perforate.
How to Choose Between Negative or Positive Mold
The choice of negative or positive mold depends on the production needs matched mold forming. If complex workpieces or larger sizes need to be produced, negative mold thermoforming is more suitable. If you need to produce simple geometries or products with high surface quality, or if you require high production efficiency, then positive mold is more suitable.
Overall, both negative and positive mold have their own advantages and disadvantages, different situations to choose different processing methods to better meet the production needs.
Process Requirements
De-molding Slope
In order to be able to release the mold smoothly, the sides of the mold must have a certain degree of inclination. In the direction of demolding, the inclination of the side of the mold is called demolding inclination. Demolding inclination should be made as large as possible, the larger the demolding inclination, the faster the demolding, the shorter the molding cycle, and in the process of demolding the product deformation possibility is small, demolding inclination is generally greater than 1 degree.
Aspect Ratio
The ratio of the width of the mold to its depth is usually called the aspect ratio. Generally speaking, because the male mold can have drag and pre-stretching effect on the sheet, the height of molding with the male mold can be slightly smaller, but not less than 1. The width-to-height ratio of molding with the female mold is usually not less than 1.4.
Forming Area and Product Area
Forming area refers to the range of length and width area inside the clamping frame, product area refers to the area where traction stretching occurs during the molding process, which mainly depends on the specification size of the thermoforming product. In the heating process, the stretching part needs to be heated, and its stretching range is larger, and for the non-product area with less heating, the amount of stretching is also smaller. It should be noted that uneven heating will also cause the problem of uneven shrinkage and deformation of the thermoforming product after molding and cooling.
Exhaust Surfaces, Exhaust Holes, Exhaust Slots
In the vacuum forming process, in order to remove the gas stored between the plastic material and the mold, the mold must be able to exhaust or have enough exhaust holes or exhaust grooves; this allows the air to be removed quickly through the extraction device (or transfer).
Therefore, in the thermoforming process, it is necessary to ensure that the vacuum system of the vacuum forming equipment can maintain a sufficient amount of vacuum to ensure that the plastic sheet is heated and softened, there can be enough vacuum suction is the plastic material can be completely adhered to the surface of the mold.
On the other hand, it is necessary to exhaust holes, exhaust grooves and other channel systems to maintain a smooth state, to avoid clogging due to foreign objects leading to a reduction in the degree of vacuum, resulting in the pressure forming is not in place.
Shrinkage Deformation of Thermoforming
In the process of thermoforming production, there will be frequent cases of product shrinkage and deformation, which need special treatment for different situations. After heating the molding, cooling stage through the mold shaping and maintain the amount of vacuum, can make the size of the thermoforming products will not change too much, but after demolding due to temperature changes, the size of the contraction deformation will occur to a certain extent, and will be with the increase in time contraction deformation will be greater. After 24 hours of molding, the shrinkage situation is basically stable, and the size measured at this time is more accurate.
Application
Thermoforming Automotive Industry
Automobile interior parts, motorcycle decorative plate, electric scooter shell, car hood, logistics turnover tray, tool car shell.
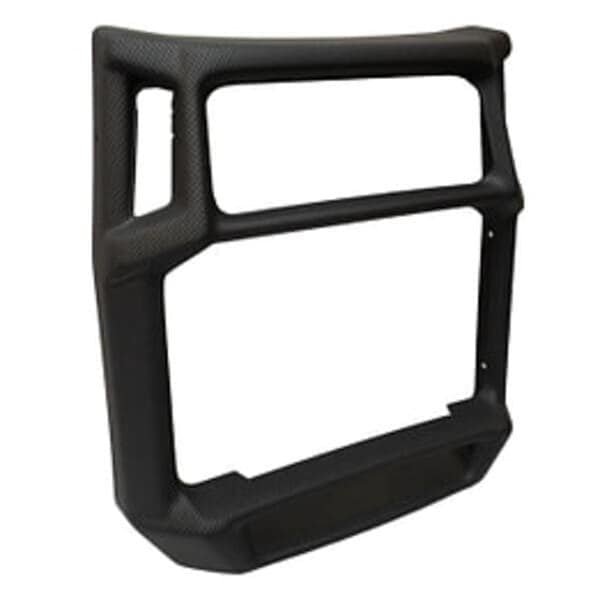
Food, Medical, Home Appliance industry Thermoforming
Thermoforming food trays (egg trays, fast food containers, cup lids, food preservation trays, etc.), cosmetics and other thermoforming packaging, refrigerator liner thermoforming, bathtubs, electronic trays, door panels, medical appliances, lamps, etc.
With the development of plastic thermoforming industry, the thermoforming of the application field is also more and more extensive, from the beginning of the thin sheet of thermoforming to the current alternative to the injection molding machine products of the thick sheet of thermoforming, from simple thermoforming of food trays, electronic trays to the current logistics thermoforming turnover trays, hardware, plastic, and so on. From the simple thermoforming food tray, electronic tray to the current logistics thermoforming turnover tray, hardware tools car, cooling water tower piece, bathtubs, and to the inward ride of the car's thermoforming parts and so on, from the original thermoforming packaging products to become a part of the product thermoforming, it can be said that now plastic thermoforming products are everywhere in our lives.
Conclusion
Pressure forming process as a very mature thermoforming technology has reached a wide range of applications, in the use of its advantages are low mold processing costs, production time is short, high production efficiency, high output per unit of time; no exhaust, wastewater, waste emissions, in line with environmental protection requirements; can be made into a variety of shaped packages and transparent packaging, to solve the shortcomings of the paper packaging; suitable for mechanization, automation of the packaging, saving manpower.
With the development of plastic thermoforming industry, the thermoforming application field is also more and more extensive, from the beginning of the thin sheet thermoforming to the present can replace the injection molding machine products of thick plate thermoforming, from the simple thermoforming food trays, electronic trays to the present logistics thermoforming turnover trays, hardware tool carts, cooling water towers, bathtubs and inwardly ride the automobile's thermoforming parts, and so on, from the original thermoforming packaging products to become a part of the products of the thermoforming, it can be said that now the plastic thermoforming products are ubiquitous in our lives.
What's Your Reaction?






