Precision Metal Stamping: What You Need to Know
Discover the essentials of precision metal stamping - from techniques to applications. Explore what makes it a crucial manufacturing process. Read now!
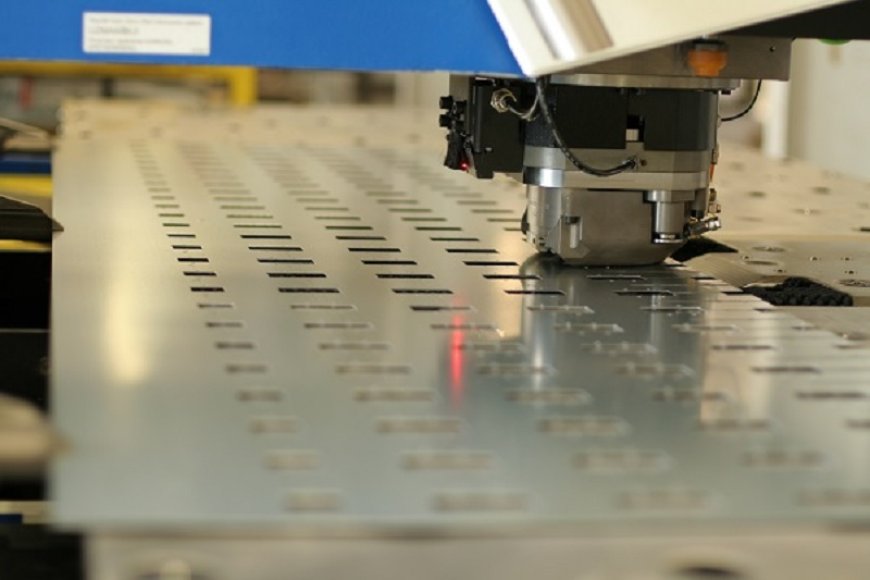
Precision metal stamping is a standard technique several sectors use to create unique metal components.
In progressive metal stamping, a “progressive die” with multiple stamping stations is used to work simultaneously on a strip of sheet metal. A feeding system unwinds the strip from its coil and pushes it through each die’s workstations until the final part is made.
Because this process uses different materials and methods, knowing your options and things to think about is essential before you start.
Problems with Precision Metal Stamping
A report by Research and Markets says that by 2027, the global market for metal stamping will be worth $250 billion. With more people wanting precision metal stamping and tools and materials changing, the industry has to change to meet new challenges. Modern methods for rolling metal are more advanced than older methods, but manufacturers still run into some of the same problems during production.
One of these common problems is metal cracking along the edges, which can happen when the metal is rolled hot or cold. Inconsistent rolling or heating can cause this, but additional metallurgical considerations must be considered.
The cold hardening index of austenitic stainless steel (0.34% for SS) is high. Austenitic stainless steel is a meta-stable type that changes when bent, causing a martensitic phase. The martensite phase is hard and cracks easily. During plastic deformation, as the amount of extension goes up, the amount of martensitic will go up, and the amount of residual stress will also go up. The more of a link there is between martensite content and residual stress, the more residual stress there is and the easier it is for processing to cause cracks.
The best way to deal with cracking in precision metal stamping, like most other problems, is to find and fix the root cause. Stampers can do root cause analysis and solve problems like these much better when they work with a precision reroll mill that knows a lot about metallurgy.
Precision Metal Stamping Uses Different Kinds of Steel
Precision metal stampings can be made from a wide range of metals. However, certain metals and methods are better suited to the precision metal stamping process or application.
Hot-rolled steel has a rough surface because it is rolled at high temperatures and cooled quickly. Cold finishing techniques are used to do more work on sheet metal at room temperature. It is done for tasks that need more precise sizes and measurements.
During cold rolling, the metal is under mechanical stress, which changes its crystalline structure in a way that can’t be reversed. It makes it more robust and often makes it more resistant to corrosion. A cold-rolled stainless-steel coil can be made with great accuracy, which lets the metal be made to very tight standards. Stamping dies are used to shape metal during precision stamping. Most of the time, this happens at room temperature, which makes it a cold process.
Compared to hot-rolled steel, cold-rolled steel has the following qualities that make it perfect for the growing needs of precision metal stampers:
- Surfaces with a smooth finish
- Dimensional uniformity (width, thickness)
- Precise edges and flatness
- Material properties that are the same and can be predicted
- More strength and hardness
Conclusion
When picking a metal to use, you should consider each part’s pros and cons and the needs of your part. It’s all about ensuring that the alloy’s properties match the application’s needs. Collaboration between stampers and precision re-rollers is beneficial, especially when developing new products and processes for precision metal stamping.
What's Your Reaction?






