Transcending Quality Thresholds: The ISO 9001 Certification Panacea
quality management system,ISO 9001 certification,
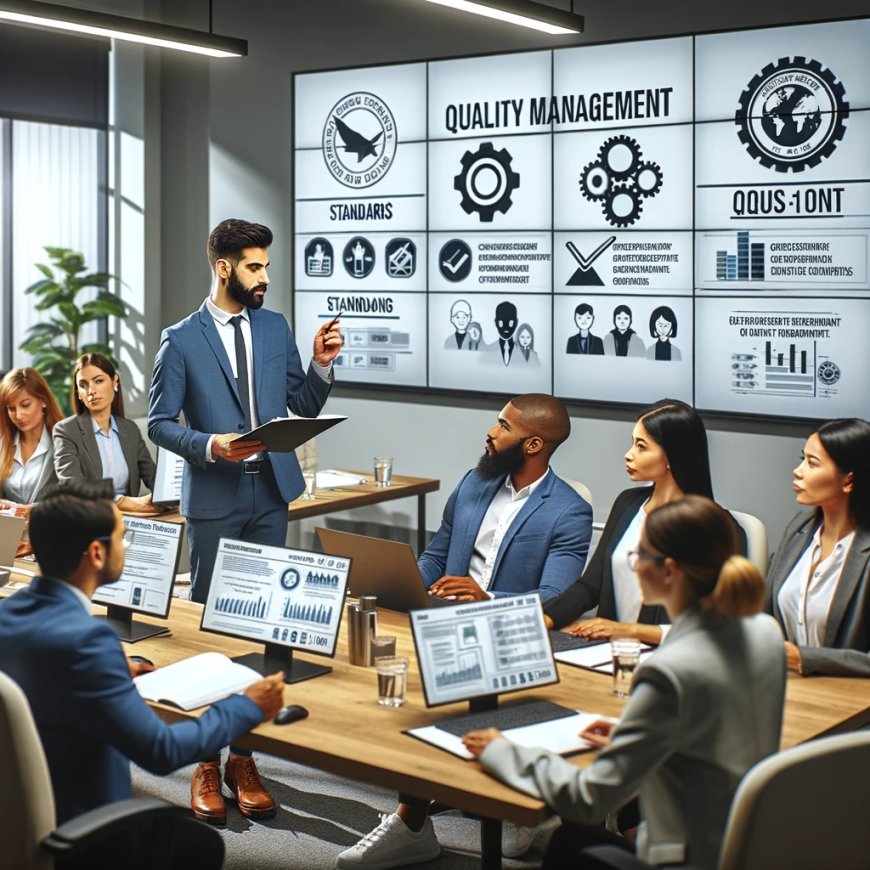
I. Introduction
A. What is ISO 9001?
ISO 9001 is an internationally recognized standard that sets out the criteria for a quality management system (QMS). It provides a framework for organizations to ensure consistent quality in products and services, enhancing customer satisfaction and trust. Compliance with ISO 9001 demonstrates a commitment to meeting customer requirements and continuously improving processes.
B. Importance of ISO 9001 Certification
ISO 9001 certification signifies that an organization has implemented a robust quality management system that meets international standards. It enhances credibility and trust with customers, suppliers, and stakeholders, leading to increased business opportunities and competitiveness in the market. Certification also enables organizations to identify and address areas for improvement systematically, driving efficiency and profitability.
C. Purpose of the Blog
This blog aims to demystify the ISO 9001 certification process, providing comprehensive guidance and insights for organizations seeking certification or looking to improve their existing quality management systems. It will explore the principles, benefits, challenges, and best practices associated with ISO 9001 certification, empowering readers to navigate the certification journey successfully and leverage quality management for sustainable growth and success.
II. Understanding ISO 9001
A. History and Background
ISO 9001 originated from the British Standard BS 5750, which aimed to standardize quality management practices. The International Organization for Standardization (ISO) adopted it in 1987, leading to the creation of ISO 9000 series standards. Since then, ISO 9001 has undergone several revisions to adapt to evolving business environments and quality management concepts, with the latest version being ISO 9001:2015.
B. Principles of ISO 9001
ISO 9001 is built on seven quality management principles:
-
Customer Focus: Prioritize understanding and meeting customer needs for satisfaction and loyalty.
-
Leadership: Set a clear vision, values, and culture that prioritize quality and empower employees.
-
Engagement of People: Involve and empower employees at all levels to contribute to quality improvement initiatives.
-
Process Approach: View activities as interconnected processes to optimize efficiency and effectiveness.
-
Improvement: Continuously seek opportunities to enhance products, services, and processes for ongoing success.
-
Evidence-Based Decision Making: Base decisions on data and analysis to ensure effectiveness and mitigate risks.
-
Relationship Management: Foster mutually beneficial relationships with stakeholders for collaboration, trust, and long-term success.
These principles provide a foundation for effective quality management, guiding organizations in achieving customer satisfaction, continuous improvement, and sustainable success.
C. Scope and Application
ISO 9001 is applicable to organizations of all sizes and industries, whether in manufacturing, services, or public sectors. It sets out requirements for establishing, implementing, maintaining, and continually improving a quality management system (QMS). The standard focuses on meeting customer requirements, enhancing satisfaction, and ensuring conformity to applicable statutory and regulatory requirements. Its flexible framework allows organizations to tailor the QMS to their specific context and objectives.
III. Benefits of ISO 9001 Certification
A. Improved Quality Management
ISO 9001 certification helps organizations establish a structured quality management system (QMS) that standardizes processes and practices. This leads to more consistent and reliable product and service quality, reducing defects and variations. The QMS also facilitates better resource management, effective problem-solving, and enhanced operational efficiency, ultimately fostering a culture of quality throughout the organization.
B. Enhanced Customer Satisfaction
By focusing on meeting customer requirements and exceeding expectations, ISO 9001 certification directly contributes to increased customer satisfaction. Organizations can more effectively address customer feedback, ensure timely delivery of high-quality products or services, and build stronger customer relationships. Satisfied customers are more likely to become repeat buyers and advocates for the organization.
C. Competitive Advantage
Achieving ISO 9001 certification signals to customers, partners, and stakeholders that an organization is committed to quality. This certification can differentiate the organization in the marketplace, enhance its reputation, and open up new business opportunities, including access to markets that require ISO 9001 compliance. It also instills confidence in potential clients and partners.
D. Regulatory Compliance
ISO 9001 helps organizations ensure compliance with relevant legal and regulatory requirements by providing a systematic approach to identify and address these obligations. This reduces the risk of non-compliance, potential legal issues, and associated penalties. The certification process often uncovers gaps in compliance, allowing for timely corrections and ongoing adherence.
E. Continuous Improvement
ISO 9001 emphasizes the importance of continuous improvement through regular monitoring, measurement, and analysis of processes. Organizations are encouraged to set improvement objectives, implement changes based on data-driven insights, and review outcomes. This ongoing cycle of improvement helps organizations stay agile, innovate, and adapt to changing market conditions, driving long-term success.
IV. ISO 9001 Certification Process
A. Step by Step Guide to ISO 9001 Certification
Preparation and Planning:
Begin by understanding the ISO 9001 requirements and assessing your organization's readiness. Assign responsibilities, allocate resources, and establish a project plan. Engage top management and ensure their commitment to the certification process.
Gap Analysis:
Conduct a thorough gap analysis to compare your current quality management system (QMS) against ISO 9001 standards. Identify areas of non-compliance and develop an action plan to address these gaps, prioritizing critical issues.
Documentation Development:
Create and update necessary documentation, including the quality manual, procedures, work instructions, and records. Ensure that these documents align with ISO 9001 requirements and accurately reflect your organization's processes and practices.
Implementation:
Implement the changes identified in the gap analysis. Train employees on the new or revised procedures and ensure that they understand their roles and responsibilities within the QMS. Foster a culture of quality and continuous improvement throughout the organization.
Internal Audit:
Conduct internal audits to evaluate the effectiveness of the QMS and ensure compliance with ISO 9001 standards. Identify any non-conformities and take corrective actions to address them. Use audit findings to drive further improvements.
Management Review:
Perform a management review to assess the performance of the QMS. Review audit results, customer feedback, process performance, and improvement initiatives. Ensure that top management is engaged and committed to addressing any issues and driving continual improvement.
Certification Audit:
The certification audit, conducted by an accredited certification body, occurs in two main phases. The initial phase involves a review of the organization's documentation and readiness, ensuring that the quality management system (QMS) meets ISO 9001 requirements. The subsequent phase is an on-site audit where the implementation and effectiveness of the QMS are evaluated. During this phase, auditors assess processes, interview staff, and review records to confirm compliance.
Continual Improvement and Surveillance Audits:
After achieving certification, maintain and continually improve your QMS. Conduct regular internal audits, management reviews, and address customer feedback. Certification bodies will perform periodic surveillance audits to ensure ongoing compliance and effectiveness of the QMS. Prepare for recertification every three years.
V. Challenges and Pitfalls
A. Common Challenges in Implementation
Implementing ISO 9001 can be challenging due to resource constraints, lack of expertise, and resistance to change. Organizations may struggle with documenting processes, aligning existing practices with ISO 9001 requirements, and ensuring consistent application across all departments. Additionally, the initial cost and time investment can be significant, requiring careful planning and prioritization to balance certification efforts with ongoing operational needs.
B. Overcoming Resistance
Resistance to change is a common obstacle when implementing ISO 9001. To overcome this, organizations should engage employees early in the process, clearly communicate the benefits of certification, and provide adequate training. Involving staff in decision-making and recognizing their contributions can foster a sense of ownership and commitment. Leadership support and a transparent approach to addressing concerns are crucial for mitigating resistance.
C. Addressing Non-conformities
Non-conformities identified during internal or external audits can pose significant challenges. To effectively address them, organizations should conduct thorough root cause analyses, implement corrective actions, and monitor the effectiveness of these actions. Continuous communication and follow-up are essential to ensure that non-conformities are resolved and do not recur. Emphasizing a culture of learning and improvement helps prevent future issues and enhances overall compliance.
VI. Conclusion
A. Recap of Key Points
ISO 9001 certification enhances quality management, customer satisfaction, and competitive advantage while ensuring regulatory compliance and promoting continuous improvement. The certification process involves preparation, gap analysis, documentation, implementation, audits, and continual improvement. Overcoming challenges like resistance and non-conformities is crucial for successful implementation.
B. Final Thoughts on ISO 9001 Certification
Achieving ISO 9001 certification demonstrates a commitment to quality and operational excellence. It fosters trust with customers and stakeholders, driving business growth. Despite challenges, the benefits of a well-implemented QMS, including improved efficiency and market competitiveness, make the certification journey worthwhile.
C. Future Trends and Developments
Future trends in ISO 9001 may include greater integration of digital technologies, increased focus on risk management, and enhanced alignment with sustainability goals. Organizations can expect evolving standards that address emerging quality management challenges, ensuring that ISO 9001 remains relevant and valuable in a rapidly changing business environment.
What's Your Reaction?






