Everything You Need to Know about Thermoforming
Discover the versatility of thermoforming and vacuum forming techniques for creating custom plastic parts. Learn about their applications, advantages, and how they can benefit your manufacturing processes. Discover the versatility of thermoforming and vacuum forming techniques for creating custom plastic parts. Learn about their applications, advantages, and how they can benefit your manufacturing processes.
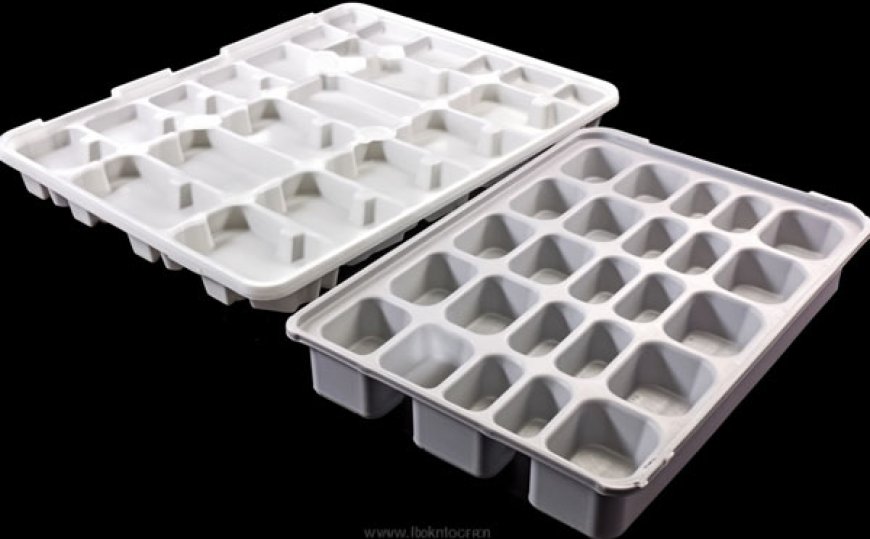
Thermoforming technology is one of the most commonly used molding methods in molded plastic material packaging, it is a thermoplastic sheet (PP/PET/PS/ABS/PVC/PE) as the molding object of the molding technology.
Although the thermoforming process has been developed in the early 20th century, it was not until the 1960s that it began to be vigorously applied to industrial production.
After continuous development and changes, the vacuum forming process has now achieved a high degree of automation and mechanization, through the continuous improvement of the thermoforming equipment, improve the temperature control of the thermoforming machine and the transmission method of the technical difficulties, to solve the high tensile and high-precision pressure forming products process technology, including solving the processing of different plastic materials as well as the thick sheet material processing technology problems.
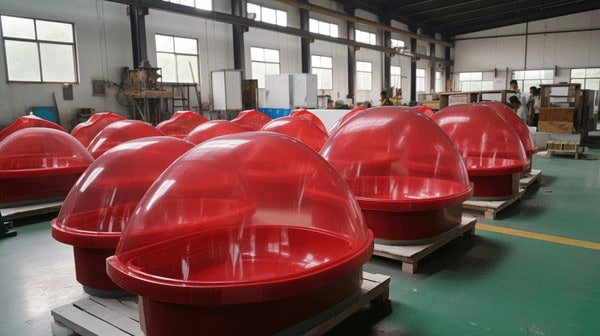
With the development of the plastic thermoforming industry, thermoforming application areas are becoming more and more extensive, from the beginning of the thin sheet of thermoforming to the present can replace the injection molding machine products of thick plate thermoforming, from the simple thermoforming food trays, electronic trays to the present logistics thermoforming turnover trays, hardware tool carts, cooling water towers, bathtubs, and inwardly ride the car's thermoforming parts and so on, from the original thermoforming packaging products to become a part of the thermoforming product, can say that now plastic thermoforming products are everywhere in our lives. It can be said that now plastic thermoforming products are everywhere in our lives.
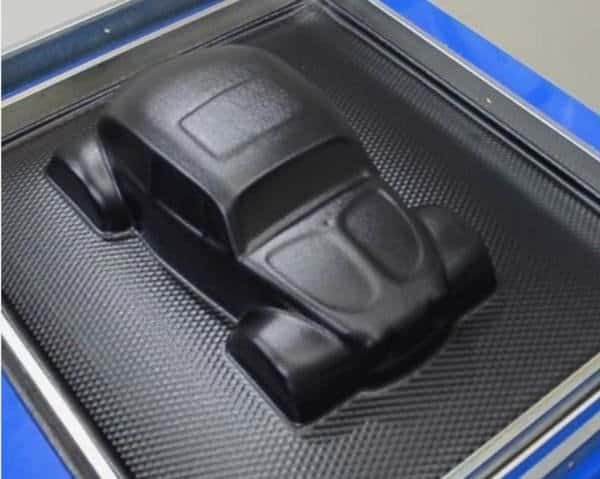
Principles of Thermoforming Process
Thermoforming process is a common plastic processing process, which is a process of heating and softening plastic sheet or plastic film, then adsorbing it on the surface of the mold by suction or pressure, and then cooling and molding it. vacuum forming process is widely used in the manufacture of various plastic products, such as plastic pallets, plastic boxes, plastic tableware, plastic toys and so on.
The principle of thermoforming process is to heat the plastic sheet or plastic film to a certain temperature to make it soften, and then adsorb it on the surface of the mold by suction or pressure to form the desired shape. The mold for the suction molding process usually consists of two parts, the upper mold and the lower mold. The space between the upper and lower molds is the molding space. In the pressure forming process, the space between the upper and lower molds is usually an air-tight space where plastic sheets or plastic films are adsorbed onto the surface of the mold by suction or air pressure to form the desired final shape or plastic components.
Commonly Used Materials for Thermoforming
Commonly used materials for thermoforming: PVC, PS, PET, PP.
PVC
PVC sheet is a widely used and popular materials, PVC film can be divided into food grade and industrial grade two kinds, and can be made into transparent, color, anti-static, gold-plated, flocking and other kinds of sheet with the sub vacuum forming, which is mainly characterized by high transparency, good surface luster, less crystalline and easy to sub molding, made of products with a small water line, the use of plant impact resistance, the Taiwan U.S. FDA, Japan's PL Food hygiene standards, made of products widely used in toys, food, electronic products, medicine, electrical appliances, gifts, cosmetics, stationery and other products packaging.
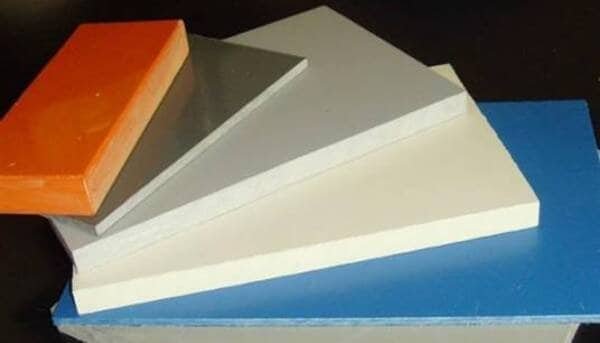
PS
PS hard sheet low density, poor toughness, easy to burn, combustion will produce styrene gas (a harmful gas), so generally used in the production of a variety of industrial trays.
Applications:
PS sheet is a new type of environmentally friendly packaging material developed in recent years. With its excellent vacuum molding performance, good impact resistance, environmental performance and hygiene performance, it is widely used in the fields of medicine, food, toys, electronics and clothing.
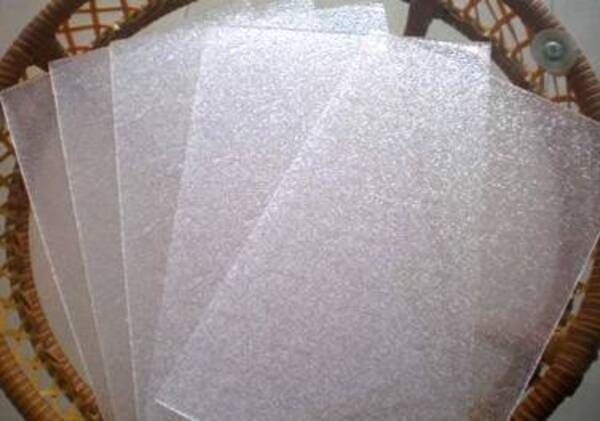
PET
Good toughness, high transparency, easy to burn, burning will not produce harmful gases, is an environmentally friendly material. But the price is high, suitable for high-grade products, Europe and the United States, the bubble shell is generally required to use PET hard sheet. But it is not easy to heat sealing, encapsulation is more difficult, in order to solve this problem, people in the PET surface composite on a layer of PVC film, named PETG hard sheet, but the price is higher.
PET important features:
1. Excellent transparency and finish, good display effect.
2. Excellent surface decorative properties, can be printed without surface treatment, easy to press patterns, easy metal processing (vacuum plating metal layer).
3. Good mechanical strength.
4. Good barrier performance to oxygen and water vapor.
5. Good chemical resistance, can withstand the erosion of a variety of chemical substances.
6. Non-toxic, reliable hygiene performance, can be used for food, drugs and medical equipment packaging, and can be Y-ray sterilization of its packaging items.
7. Good adaptability to environmental protection, can be economically and conveniently recycled; its waste incineration treatment, does not produce environmentally harmful substances. Good thermoforming performance, comparable to ordinary PVC sheet, can be vacuum-formed to produce PET thermoforming products with excellent performance; PET sheet is considered to be the ideal packaging material in line with environmental requirements.
.jpg)
PP
PP sheet is made of PP resin through the process of beer, calendaring, cutting edge, etc. It has the characteristics of light weight, bright and calm surface, good heat resistance, high mechanical strength, excellent chemical stability and electrical adiabaticity, and non-toxicity, etc. It can be made into beverage cups, food containers, and other daily necessities after thermoforming.
PP main features:
Can be used for a long time at 100 ℃ and can withstand 121 ℃ high temperature sterilization treatment, moisture-proof performance is outstanding, reliable health performance, widely used in food packaging. It has excellent folding performance.
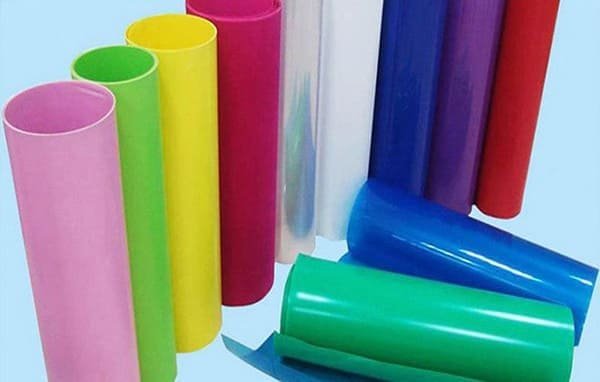
What are the Steps of Thermoforming Process
Mold Design and Production
Molds are key to the manufacturing process of thermoformed products. It needs to be made by hand or CNC machining, etc., taking into account the size and shape requirements of the product as well as the process flow.
According to user requirements or sample specifications, the first production of good plastic molds, general conditions, are the use of gypsum production of plastic molds, but there are also wood and metal carving products for the mold, plastic production molds with the lowest cost of gypsum molds, followed by plating of copper molds, the most expensive is the aluminum mold.
Gypsum molds made after the first to let it dry naturally or dry completely, and then according to the product surface convex and concave specifics, with 1-2 mm drilling flower does not affect the product packaging model of the low-concave drilling of many small holes, if it is a product such as boxes, but also have to be drilled around the edges of a number of small holes, so that the production of thermoforming, can be pumped out of the air, the mold drilled holes, but also have to be gypsum molds hardening, hardening treatment! The method is to soak the molds in a thick liquid solution of isotopes and then dry them.
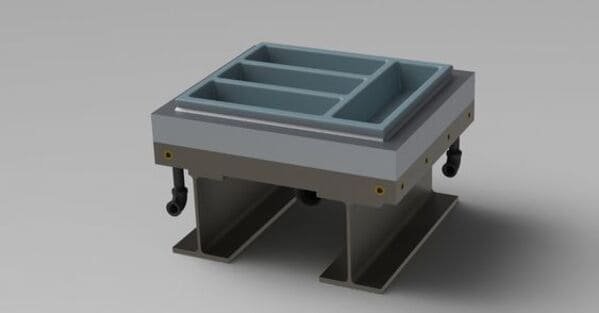
Material Selection
According to the material requirements of the product, choose the appropriate plastic sheet material common plastic sheet material are PVC, PE, PET and so on. Before molding thermoforming, the plastic sheet needs to be cut and trimmed to match the mold.
Heating Plastic Sheets
Add the raw material into the thermoforming machine equipment for heating. Melting temperature and time according to different raw materials and product requirements, generally between 150 ° C and 200 ° C. When heated, the raw material gradually soften, transformed into a better plasticity condition.
Forming
The softened plastic is placed over the top of the mold and an air compressor is started to suck out the gas from the mold to rapidly forming plastic sheets. This step keeps the plastic tight against the mold surface for better molding.
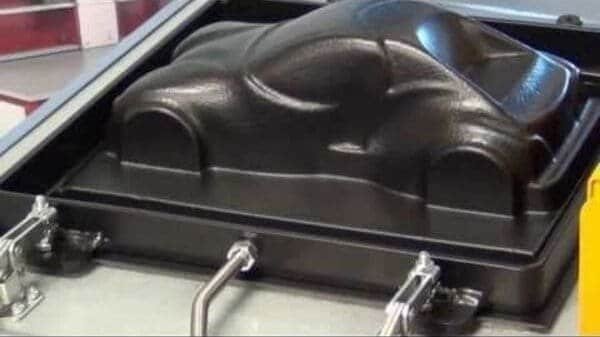
Cooling
After the plastic softens and forms, the cooling and solidification process begins. This process requires uniform temperature and pressure on the plastic sheets surface and interior of the plastic to achieve the final effect.
Removing the Product
After the plastic has completely cooled, open the mold and remove the molded components.
Trimming and Polishing
Trim and shape the removed molded components, removing excess plastic and trimming the edges.
Quality Control
Check the appearance quality and size accuracy of the molded products to ensure they meet customer's requirements.
Thermoforming Machine Operation
The thermoforming machine is the core equipment for thermoforming production. During operation, the corresponding workpiece needs to be made according to the size and shape of the product, the material is placed into the upper mold of the thermoforming machine, and the lower mold is placed on the material. Then turn on the heating plate for heating, which is usually completed within 2-5 minutes. Pay attention to the temperature and time during the heating process to avoid overheating or overcooling. After the heating time is over, turn off the heating plate and suck into the lower mold to form the material.
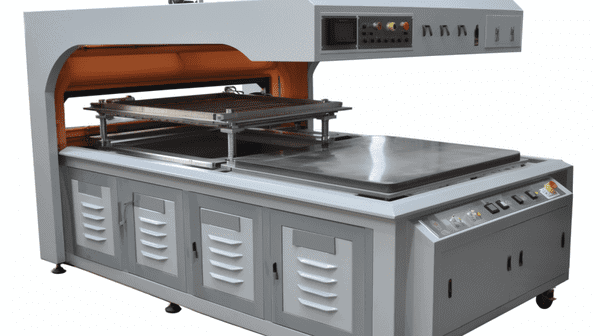
Thermoforming vs. Injection Molding
Injection Molding
1. Advantages: Stable product quality: The injection molding machine automatically controls the temperature, pressure, time and other factors to produce stable product quality and meet the requirements. Injection molding processing with higher pressure can produce precise products with good surface quality and high precision.
At the same time, injection molding is highly variable and applicable to a wide range of materials, including thermoplastics, thermosets and rubber, etc., and automated production can be realized. The injection molding process adopts plastic granules as raw materials, avoiding environmental problems such as dust, waste water and exhaust gas produced by traditional processing methods, and meeting the requirements of environmental protection.
2. Disadvantages: High investment is needed to purchase injection molding machines and molds, and the production process of products requires high technical level and production experience. In addition, the service life of injection molding machine is relatively short and the maintenance cost is high.
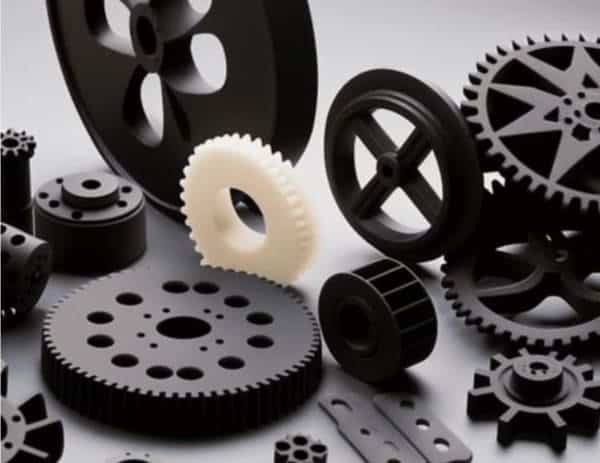
Thermoforming
1. Advantages: The advantages of thermoforming process are low cost, high production efficiency, short manufacturing cycle, simple production process, high manufacturing precision, stable product quality and so on. Thermoforming process can produce a variety of shapes of plastic products, such as flat, three-dimensional, curved surface, etc., can meet the needs of different customers. Thermoforming process of plastic products have good wear resistance, corrosion resistance, high temperature resistance, low temperature resistance, pressure resistance and other characteristics, widely used in various fields.
Thermoforming process method is simple, the equipment needed is simpler than injection molding, the cost is also lower, the process requirements are lower, the fault tolerance rate is high, and the processing process can be quickly adjusted. Moreover, thermoforming can produce larger size products, which is applicable to a wide range of products.
2. Disadvantages: Thermoforming processing pressure is low, precision and surface quality is relatively poor compared to injection molding. At the same time, can only process thermoplastic plastics, and thermosetting plastics and other materials are not applicable.
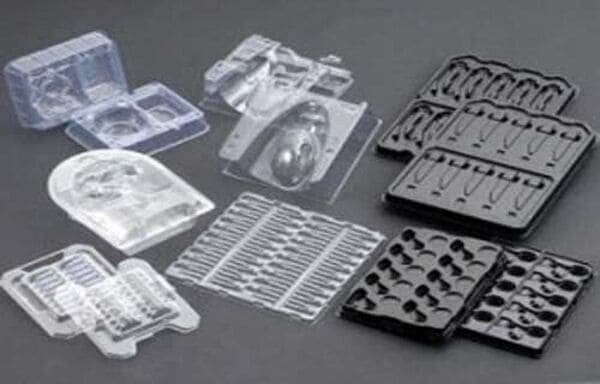
Comparison of Injection Molding and Thermoforming
Injection molding requires high investment, but the surface quality of the product is good and the precision is high, while the cost of thermoforming is relatively low, but the surface quality and precision are worse.
The material variability of injection molding can be strong, while automated production can be realized, while the thermoforming process can only process thermoplastic materials.
Injection molding processing requires a higher level of craftsmanship than thermoforming processing.
Application of Thermoforming
Thermoforming products have a wide range of applications. Thermoforming products can be made into different shapes and sizes according to the needs of the products, which are suitable for different fields.
For example, it can be used to make furniture and daily necessities in the household field, electronic shells and panels in the electronic field, medical devices and packaging in the medical field, and automobile parts and interior decoration in the automobile field. With the continuous development of various fields, the demand for vacuum forming products will be more and more, which provides a broad market space for the development of the thermoforming industry.
Thermoforming process has a wide range of applications, mainly used in the following areas
1. Packaging industry: Thermoforming can produce a variety of shapes of plastic food packaging boxes, plastic trays, plastic bags, etc., widely used in food, medicine, cosmetics, electronic products and other industries.
2. Household industry: Thermoforming can produce a variety of shapes of plastic household goods, such as plastic chairs, plastic tables, plastic storage boxes, etc.
3. Toy industry: Pressure forming can produce a variety of shapes of plastic toys, such as plastic blocks, plastic puzzles, plastic models, etc.
4. Automotive industry: Thermoforming can produce various shapes of automotive interior parts, automotive exterior parts, automotive parts and so on with vacuuming forming, pressure forming or twin sheet forming.
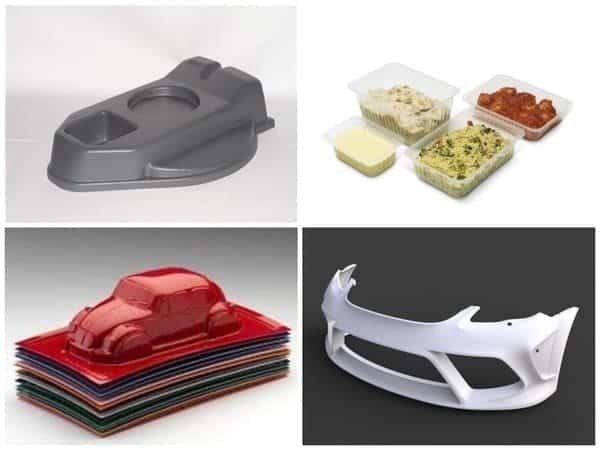
Conclusion
The continuous innovation and development of thermoforming technology provides new opportunities for the thermoforming industry With the progress of science and technology and the change of product demand, thermoforming technology is also constantly innovating and improving.
At present, with the enhancement of environmental protection consciousness, green and environmentally friendly thermoforming materials and manufacturing processes have become the hotspot of the industry. Based on this, the thermoforming molding industry can develop environmentally friendly thermoforming molding products by introducing new materials and processes to meet the market demand and gain a competitive advantage.
The specialization level of the thermoforming industry in terms of process and equipment is also improving With the continuous development of the thermoforming process, the performance of the thermoforming machinery and equipment is also improving the degree of automation, the production efficiency and product quality have also been significantly improved At the same time, the specialization of the thermoforming technology is also becoming more and more demanding, requiring practitioners to have the relevant professional knowledge and skills. These positive factors will further promote the development of the thermoforming industry.
As an important method of manufacturing plastic products, thermoforming has a wide range of applications, good performance and quality as well as opportunities for continuous innovation and development. With the development of various industries and growing consumer demand, the thermoforming industry is expected to achieve greater development in the future.
However, it should be noted that the thermoforming industry is also facing challenges such as intensified market competition and technological upgrading, and it needs to continuously improve its competitiveness and innovation ability in order to achieve an advantageous position in the fierce market competition.
What's Your Reaction?






