High-Quality Welding Equipment for Professionals
Explore TECHWELD's premium welding equipment for top performance and reliability. Find the perfect welding tools to suit your needs today!
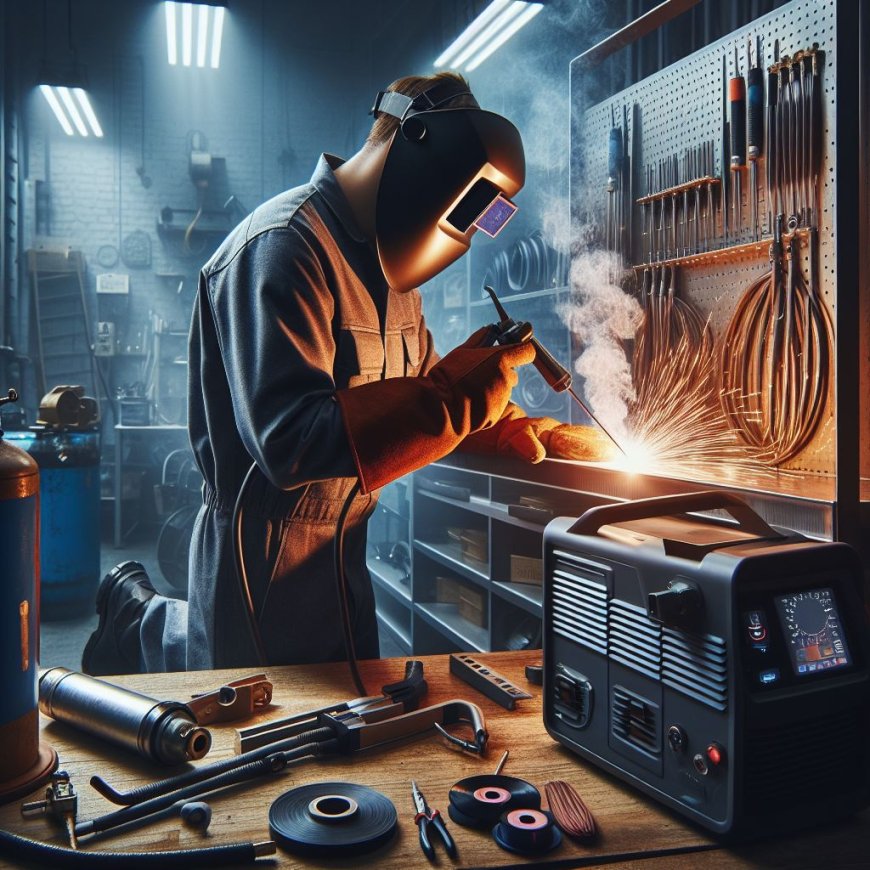
When it comes to welding, the equipment you use can make all the difference. Whether you're a seasoned professional or an aspiring welder, having reliable and high-quality welding equipment sets the foundation for achieving exceptional results. Imagine running a bead of weld that is smooth, consistent, and exceptionally durable – it's all possible with the right tools. In this comprehensive guide, we'll explore the importance of choosing top-notch welding equipment and how it can elevate your craft.
Why Quality Matters in Welding Equipment
Safety First
The primary reason to invest in high-quality welding equipment is safety. Welding involves intense heat and requires precision. Sub-par tools can lead to accidents, injuries, and even catastrophic failures. A well-crafted welding machine ensures stable performance, reducing the risk of malfunctions that could lead to burns, electric shocks, or harmful fumes.
Enhanced Performance
High-quality welding equipment provides consistent and reliable performance. This consistency is critical for producing strong, clean welds. Premium tools are engineered to maintain stable arc characteristics, which enhances the quality of the weld seams. Superior equipment also offers better control over the welding process, allowing you to adjust settings with greater precision.
Durability and Longevity
Investing in durable welding equipment pays off in the long run. Cheap tools may save money upfront, but they often wear out quickly, leading to frequent replacements. High-quality welding machines and accessories are built to withstand rigorous use, ensuring they stay functional and effective for years. This means less downtime and more productivity on the job.
Key Features of High-Quality Welding Equipment
Power and Amperage Control
Top-tier welding equipment allows for precise control over power settings and amperage. This feature is essential for different types of welding projects. Whether you’re working on thin metals or heavy-duty industrial materials, the ability to fine-tune power and amperage ensures optimal results.
Portability and Versatility
Modern welding equipment is designed with portability in mind. Lightweight and easy-to-transport machines enable welders to work in various locations without hassle. Furthermore, versatile equipment that can handle multiple welding processes (like MIG, TIG, and Stick welding) adds value by allowing you to switch between techniques as needed.
Advanced Technology
Innovations in welding technology have led to the development of advanced features like inverter technology, digital interfaces, and automatic adjustments. These advancements make welding more efficient and less cumbersome. For instance, inverter technology offers better energy efficiency and smoother arc performance, while digital interfaces provide intuitive controls and feedback.
Types of Welding Equipment
MIG Welders
MIG (Metal Inert Gas) welders are popular for their ease of use and versatility. They use a continuous wire feed and gas shield to create a clean and strong weld. MIG welders are ideal for both beginners and professionals due to their straightforward operation and ability to handle a wide range of materials.
TIG Welders
TIG (Tungsten Inert Gas) welders offer greater precision and control, making them perfect for intricate and high-quality welds. They are commonly used in applications requiring clean and aesthetic welds, such as aerospace and automotive industries. TIG welding is particularly effective for aluminum and stainless steel.
Stick Welders
Also known as SMAW (Shielded Metal Arc Welding), stick welders are highly versatile and can be used in various conditions, including outdoor environments. They are less sensitive to wind and contaminants, making them suitable for construction and repair work.
Choosing the Right Welding Equipment
Assess Your Needs
Before purchasing welding equipment, assess the specific needs of your projects. Consider the material types, thicknesses, and welding techniques you will use most frequently. This assessment will help you determine the most suitable type of welder.
Budget Considerations
While high-quality welding equipment can be more expensive, it’s important to consider long-term costs. Investing in a reliable machine can reduce maintenance expenses and increase productivity. Look for reputable brands known for their durability and performance.
Read Reviews and Seek Recommendations
Customer reviews and expert recommendations can provide valuable insights into the reliability and performance of different welding machines. Join welding forums, attend trade shows, and consult with experienced welders to gather information.
Maintenance Tips for Welding Equipment
Regular Inspections
Conduct regular inspections of your welding equipment to identify any signs of wear or damage. Check the cables, connections, and consumables for any issues that could affect performance.
Proper Storage
Store your welding equipment in a dry, clean environment to prevent rust and contamination. Use protective covers to shield the machines from dust and debris.
Routine Cleaning
Clean your welding equipment regularly to remove any accumulation of dust, grease, or welding spatter. This helps maintain optimal performance and extends the life of your tools.
Conclusion
Choosing high-quality welding equipment is an investment in your safety, performance, and productivity. The right tools not only enhance the quality of your work but also ensure you can tackle a wide range of welding projects with confidence. By understanding the key features, types, and maintenance tips, you'll be better equipped to select the best welding equipment for your needs. Remember, in the world of welding, quality always pays off.
Ready to upgrade your welding setup? Explore our range of premium welding equipment and take your skills to the next level.
What's Your Reaction?






