Production Part Approval Process Level 1 - Guide for Automotive Suppliers
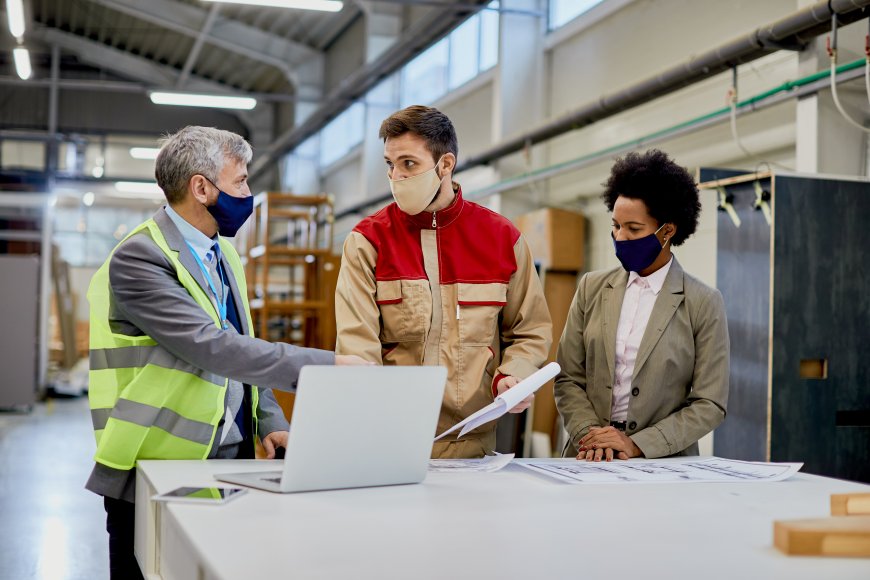
The Production Part Approval Process (PPAP) Level 1 is an essential requirement for automotive suppliers in the industry. It serves as a standardized approach to ensure that the components or parts provided by suppliers meet the quality and reliability standards of the automotive manufacturers and their customers. This guide aims to provide automotive suppliers with a comprehensive understanding of PPAP Level 1, its significance, and the necessary steps to navigate the process successfully. By following this guide, suppliers can enhance their compliance with PPAP Level 1 requirements, establish effective collaboration with OEMs and Tier 1 suppliers, and achieve successful approval for their parts in the automotive industry.
1.Introduction to Production Part Approval Process (PPAP) Level 1
1.1 What is PPAP Level 1?
So you're in the automotive business, and you've heard of this component known as PPAP Level 1. But what exactly is it? Well, my friend, PPAP stands for Production Part Approval Process, and level 1 indicates the lowest level of PPAP submission. In short, it's a sophisticated way for automotive providers to demonstrate that they can consistently produce parts that meet the needs of their clients (OEMs or Tier 1 providers).
1.2 Purpose and benefits of PPAP Level 1
You might wonder why we want a level 1 PPAP in the first vicinity. The solution is straightforward: superior control. PPAP Level 1 helps ensure that automotive suppliers have the essential strategies and documentation to deliver parts that meet OEM specifications and expectations.
By going through PPAP Level 1, suppliers not only benefit from the trust and confidence of their customers but also reduce the risk of errors and defects in their products. It's a win-win scenario for everyone involved.
2. Understanding the role of automotive suppliers in PPAP Level 1
2.1 Obligations of automotive suppliers in PPAP level 1
As a car dealer, your role in the Level 1 PPAP method is critical. You are responsible for ensuring that your manufacturing processes can consistently meet the needs targeted by OEMs or Tier 1 suppliers. This way, it has a robust, excellent management gadget in the area, engages in thorough inspections and tests, and meticulously documents the whole.
2.2 Cooperation with OEMs and Tier 1 suppliers
Collaboration is essential in the global scale of PPAP Level 1. It would help if you worked closely with OEMs and Tier 1 providers to understand their needs and expectations. Clear communication and excellent cross-country dating are essential to successfully navigating the PPAP Level 1 system. So grab your smartphone and reach out to your customers. Trust me, they might appreciate your proactive approach.
3. Key requirements and documentation for PPAP level 1
3.1 Understanding PPAP Submission Levels
PPAP contributions come in different flavors or levels, if you will. At Level 1, the focus is on ensuring that your manufacturing processes are in control and capable of producing parts that meet requirements. This includes performing process capability studies, achieving measurement repeatability and reproducibility (GR&R) studies, and providing dimensional results.
3.2 Documentation Checklist for PPAP Level 1
When it comes to PPAP Level 1, documentation is your best friend. You will need to compile a comprehensive checklist of documents to demonstrate that you meet the requirements. This includes inspection plans, process flow charts, inspection records, and material certifications. But don't worry—with a little organization and attention to detail, you'll get through this checklist like a pro.
4. Significance of Initial Sample Inspection (ISI) in PPAP Level 1
4.1 Purpose and benefits of initial sample control
Now, let's talk about Initial Sample Inspection (ISI). This step in the Production Part Approval Process Level 1 process involves verifying that the first samples produced meet all requirements. Think of it as a litmus test for your manufacturing processes. By performing an ISI, you can catch any potential problems early and ensure your parts are up to snuff immediately. This saves you time and money and helps maintain a stellar reputation with your customers.
4.2 Implementation of the initial sample control process
So, how do you do ISI? First, you will need to select representative samples from your production. These samples will be subjected to strict inspection and testing to verify that they meet the specified requirements. Any discrepancies or deviations must be addressed before proceeding with total production. It's all about that attention to detail, my friend.
And there you have it - a PPAP Level 1 guide that won't let you sleep. Remember, PPAP may sound intimidating, but with ingenuity and organization, you'll be well on your way to automotive supplier stardom. Good luck!
5.PPAP Level 1 Submission Process and Timing
5.1 Overview of the Submission Process
Navigating the PPAP Level 1 submission process doesn't have to feel like exploring uncharted territory. In this section, we'll break down the steps to help you stay on track and avoid unexpected detours.
First, familiarize yourself with the requirements listed in the PPAP manual. This will be your trusted blueprint throughout the process. Ensure you have all the necessary documents, including customer-specific requirements, control plans, and measurement system analysis (MSA) documents.
Next, it's time to assemble a team of experts. This could include individuals from quality assurance, engineering, and manufacturing. Work with them to compile the necessary information and ensure accuracy.
Once you have all the required documents, it's time to pack and send them. Be sure to keep a record of all submissions for future reference.
5.2 Timing and Deadlines for Level 1 PPAP Submissions
Timing is everything, and it is no different regarding PPAP Level 1 submission; understanding deadlines is essential to avoid any last-minute panic-induced hair-pulling.
Remember that timing requirements may vary depending on customer expectations and specific industry standards. It is essential to communicate with your customers to meet submission deadlines. Early involvement can help avoid unnecessary delays in the process.
Stay proactive and plan. Allow yourself enough time to complete all required activities and ensure accuracy and thoroughness. A rushed process can lead to avoidable mistakes or missing important information.
Remember, effective time management and open communication are the keys to success. Stay organized, meet deadlines, and keep the lines of communication open with your customers.
6. Best practices for achieving successful PPAP Level 1 approval
6.1 Implementation of robust quality management systems
Building a solid foundation is essential to success, and PPAP Level 1 is no exception. Establishing a robust quality management system is the cornerstone of achieving successful approval.
Invest time and effort in developing a quality management system that complies with industry standards and customer requirements. Ensure clear documentation and standardized processes that support effective communication and thorough record-keeping.
6.2 Implementation of effective change management processes
Change is inevitable and even more prevalent in the dynamic automotive manufacturing world. Implementing effective change management processes is paramount to successfully navigating a constantly changing environment.
Implement a systematic approach to documentation and change management throughout the manufacturing process. This includes thorough impact assessment, clear communication with stakeholders, and proper implementation and verification of changes.
6.3 Implementation of a thorough approval process for production components
The heart of PPAP Level 1 is to perform a comprehensive approval process for production parts. Take the time to ensure the process's accuracy, completeness, and efficiency.
Perform thorough dimensional and functional tests to verify product compliance. Pay attention to detail, and leave no stone unturned. Remember, the goal is to demonstrate that your manufacturing process can consistently meet customer requirements.
7. Common Challenges and Solutions in Tier 1 PPAP Implementation
7.1 Overcoming Supply Chain Complexity
Navigating the complex web of the automotive supply chain can feel like solving a Rubik's cube blindfolded. However, overcoming this complexity is critical to successfully implementing a Tier 1 PPAP.
Create clear communication channels with your suppliers and customers. Foster collaborative relationships that encourage transparency and timely information sharing.
Invest in technologies that simplify supply chain management, such as real-time tracking systems. This can help you identify and address potential bottlenecks before they run into significant obstacles.
7.2 Non-Compliance Resolution and Remedial Actions
Even the best-laid plans can go awry, and failure to follow them is often an unwelcome guest. When non-compliance issues are encountered during PPAP Level 1 implementation, it is essential to resolve them quickly and efficiently.
Establish a robust corrective action system to track and address non-compliance. Implement a root cause analysis process to identify underlying problems and develop practical solutions.
Maintain open communication with your customers throughout the process. You can promptly acknowledge and address non-compliance to maintain trust and ensure a smoother Level 1 PPAP implementation.
8. Ensuring continuous improvement of PPAP level 1 for automotive suppliers
8.1 Monitoring Key Performance Indicators (KPI)
In the fast-paced automotive industry, it's all about continuous improvement. Monitoring key performance indicators (KPIs) can provide valuable insights and lead to constant improvement of PPAP Level 1 implementation.
Identify relevant KPIs that align with your quality goals and customer requirements. Monitor and analyze these indicators regularly to identify trends, areas for improvement, and potential risk factors.
8.2 Implementation of lessons learned and best practices
Learning from past experiences and implementing best practices is essential for continuous improvement. Take the time to review and analyze completed PPAP Level 1 submissions and identify areas of success and areas for improvement.
Foster a culture of continuous learning in your organization. Share lessons learned, implement standardized processes, and provide training opportunities to ensure continuous PPAP Tier 1 implementation improvement.
Remember that success in PPAP Level 1 is an ongoing journey, not a one-time event. Stay committed to continuous improvement, embrace challenges, and celebrate successes.
Conclusion
In conclusion, the Level 1 Production Parts Approval Process (PPAP) is a critical aspect of the automotive industry that suppliers must follow closely. By following the requirements and documentation outlined in this manual, suppliers can ensure that their parts meet the necessary standards and gain the trust of automakers and customers. Successful implementation of PPAP Level 1 leads to improved quality and reliability and supports long-term relationships with OEMs and Tier 1 suppliers. Through continuous improvement and proactive measures, suppliers can thrive in the competitive automotive market and contribute to the industry's overall success.
What's Your Reaction?






