Detecting Bad Welding vs Good Welding in Industrial Applications
Detecting bad welding versus good welding in industrial applications is crucial for ensuring safety and high performance in operation. When it comes to welding, there are key indicators that can help distinguish between a well-executed weld and a subpar one.
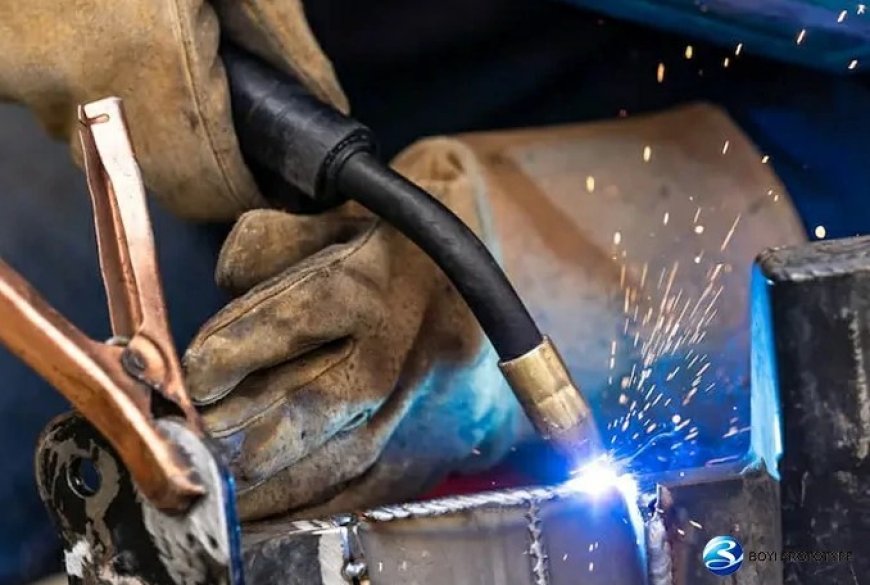
Detecting bad welding versus good welding in industrial applications is crucial for ensuring safety and high performance in operation. When it comes to welding, there are key indicators that can help distinguish between a well-executed weld and a subpar one.
One of the first things to look out for is the appearance of the weld itself. Good welding typically results in a smooth, uniform bead with consistent penetration into the base materials. In contrast, bad welding may exhibit irregularities such as undercuts, incomplete fusion, or excessive spatter. These visual cues can signal potential weaknesses in the weld that could compromise its integrity over time.
Another important factor to consider is the strength of the weld. A good weld will have strong and durable bonds that are able to withstand the demands of the bad welding vs good welding. On the other hand, bad welding may result in weak joints that are prone to cracking or breaking under stress. Conducting thorough testing, such as destructive testing or non-destructive testing, can help determine the quality and integrity of the weld.
In addition to visual and strength considerations, it is also important to pay attention to the behavior of the weld during operation. A good weld will perform reliably and consistently over time, demonstrating its ability to withstand various environmental conditions and mechanical stresses. In contrast, a bad weld may show signs of premature failure, such as cracking, distortion, or degradation of the materials.
In industrial applications, the consequences of bad welding can be severe. Weak or faulty welds can lead to structural failures, equipment malfunctions, or even safety hazards for workers. It is therefore essential for welders and inspectors to be vigilant in detecting and addressing any issues with the welding process.
To ensure good welding practices in industrial applications, proper training and certification of welders are essential. Welders should be knowledgeable about the materials they are working with, as well as the specific welding techniques required for the job. Regular inspections and quality control measures can also help prevent potential issues before they escalate.
Ultimately, the goal of detecting bad welding versus good welding in industrial applications is to ensure the safety and performance of the finished product. By paying attention to visual cues, strength testing, and operational behavior, welders and inspectors can identify and address any potential issues with the welds before they lead to costly repairs or catastrophic failures. Good welding practices are the foundation of a successful industrial operation, and it is essential to prioritize quality and safety at every step of the welding process.
In conclusion, it is clear that the quality of welding plays a crucial role in ensuring both safety and performance in any project. Poor welding practices can lead to structural failures, injuries, and even fatal accidents, while good welding techniques can result in strong, reliable joints that stand the test of time. By prioritizing proper training, equipment, and attention to detail, welders can uphold high standards of quality and ensure the success of their work. Remember, when it comes to welding, investing in quality always pays off in the long run.
What's Your Reaction?






