The Future of Spray Booth Technology: Innovations to Watch
Spray booth technology is a key component of productivity, quality, and safety in the rapidly changing industrial and automotive industries. Over the years, breakthroughs have been
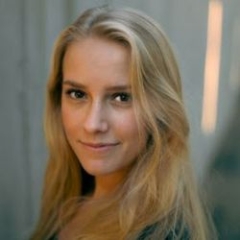
Spray booth technology is a key component of productivity, quality, and safety in the rapidly changing industrial and automotive industries. Over the years, breakthroughs have been