Choose the Right Shearing Machine for Your Workshop
Shearing machines are essential for sheet metal work to deliver precise cuts efficiently. Understanding different types, functionalities, and factors to choose from helps suit specific needs and budgets.
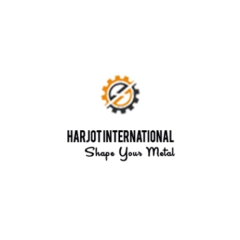