Pipe Bearing Mounting Plate: Understanding this Manufacturing Process
The manufacturing process of pipe bearing mounting plates involves a combination of materials, methods, and techniques to produce high-quality components that meet the demanding requirements of various industries.
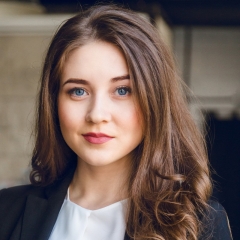