Leak Testers: Methods, Techniques, and Other Determinants
Leak testing is critical to modern manufacturing, ensuring product integrity, safety, and compliance with industry standards. From traditional methods to advanced techniques, leak testers play a vital role in preventing defects and minimising the risk of product failure.
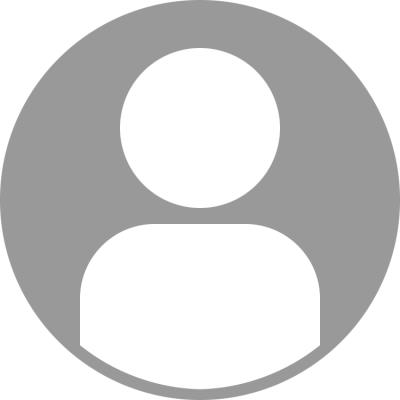