ISO 9001: The Ultimate Guide to Quality Management Systems
In today's fiercely competitive business world, maintaining high standards of quality is not just an option; it's a necessity.
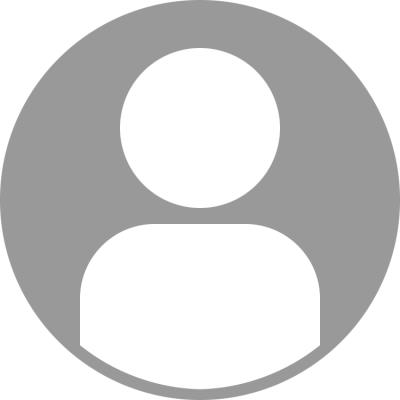
In today's fiercely competitive business world, maintaining high standards of quality is not just an option; it's a necessity.