What is Contact Resistance Meter and Why is Contact Resistance Testing Important?
The smooth flow of electricity is vital for everything from powering our homes to keeping critical infrastructure operational. But even the best-designed electrical systems can be c
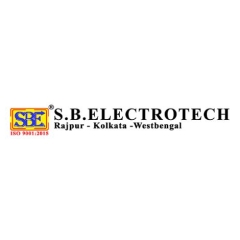