How is Technologies Helping Tool Manufacturers in India?
To achieve Industry 4.0, many technologies such as the Internet of Things (IoT), Artificial Intelligence (AI), Augmented Reality (AR), Virtual Reality (VR), Digit
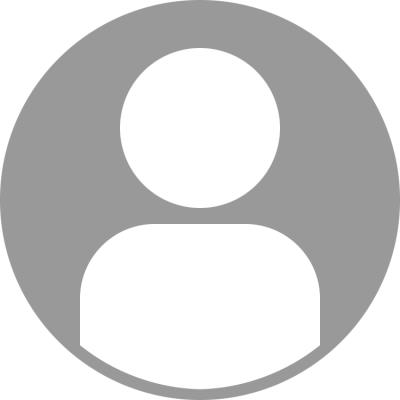
To achieve Industry 4.0, many technologies such as the Internet of Things (IoT), Artificial Intelligence (AI), Augmented Reality (AR), Virtual Reality (VR), Digit