How Hairpin Heat Exchangers Are Shaping Industrial Cooling
In the ever-evolving landscape of industrial processes, efficient cooling systems are crucial for maintaining optimal operating conditions and ensuring energy conservation.
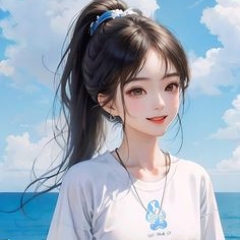
In the ever-evolving landscape of industrial processes, efficient cooling systems are crucial for maintaining optimal operating conditions and ensuring energy conservation.