Factor to Choose the Right Flux-Core Aluminum Welding Wire
You treasure utilizing flux-core wire for the comfort of not requiring extra shielding gas, but you’re adorable and sure the things you utilize on steel won’t perform. So, you go chasing for flux-core aluminum welding wire
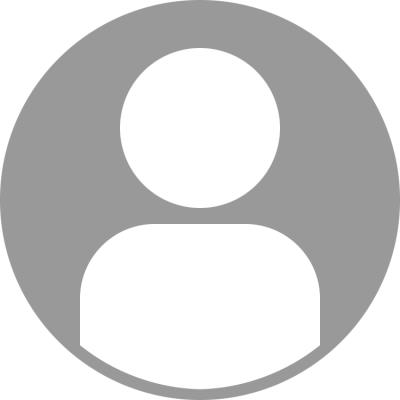